Histoire de la production de l'acier

L’histoire de la production de l'acier, comme la plupart des histoires de découvertes et progrès techniques, n'est pas linéaire. On trouve des aciers à divers endroits de la planète au cours de l'histoire. Certaines innovations apparaissent sans se répandre : l'Europe découvre l'utilisation de la houille 1 000 ans après la Chine, les Arabes ne connaissant pas ce combustible. D'autres se diffusent différemment : l'adoption de l'énergie hydraulique permet au haut fourneau d'être réinventé partout où le minerai de fer s'y révèle compatible.
Avec la Renaissance commence un inventaire des techniques, dont l'analyse se poursuit par des méthodes scientifiques jusqu'à la fin du XVIIIe siècle. Ces techniques, qui restent marquées par les contraintes locales et la transmission du savoir-faire, persisteront jusque dans la seconde moitié du XIXe siècle. C'est en effet à cette époque qu'apparaissent les innovations les plus marquantes. Toutes sont liées à la mise au point du procédé indirect : le couple constitué par le haut fourneau et le convertisseur fonde la sidérurgie moderne.
Enfin, la sidérurgie de la fin du XXe siècle est contrainte de muter brutalement. La possibilité d'utiliser massivement des énergies et des procédés jusque-là coûteux ou complexes, comme l'électricité ou l'injection d'oxygène pur, permet l'utilisation d'outils dont les performances surclassent indiscutablement ceux de la révolution industrielle.

Fer, fonte, acier, une définition changeante au cours du temps
[modifier | modifier le code]Depuis l'Âge du fer, le minerai de fer est travaillé à relativement basse température, dans un bas fourneau. On obtient une masse hétérogène, la « loupe », qui est martelée pour en enlever les scories. Les artisans remarquent très tôt que les blocs de métal obtenus n'ont pas tous les mêmes propriétés. Les progrès de la science permettent par la suite de classer les différents alliages selon leur composition chimique.
L'Antiquité
[modifier | modifier le code]Si les Grecs antiques distinguaient déjà le fer de l'acier, il est probable que la signification historique de ces deux mots soit déformée par nos connaissances actuelles[1]. En effet, deux mots coexistaient : sídēros (σιδηρος), qui désigne le fer, était aussi bien employé pour la production (mine de fer), l'usage (fabriqué en fer, tressé en fer), l'emploi (couper avec du fer) et la symbolique (dur comme fer, au cœur de fer). Il semble même que ce terme ait désigné les métaux d'une manière générale[1]. L'autre mot, khályps, khálybos (χάλυψ, χάλυβος), désigne plus précisément l'acier ; il se réfère aux Chalybes, un peuple d'Anatolie auquel Strabon attribuait l'invention de la sidérurgie[2], et serait apparenté au hatti ḫapalki et au hourrite ḫabalgi, tous deux au sens de « fer ». Selon le doxographe grec du IIIe siècle av. J.-C. Théophraste, ce serait Délas, un Phrygien, qui aurait inventé le fer[3]. Théophraste a écrit un Traité sur les métaux, dont le titre originel n'est pas sans rappeler le mot métal[4], mais le terme de Théophraste metálleuta (μετάλλευτα) désigne le mot général utilisé. La métallurgie du fer était déjà élaborée, puisque les Grecs pratiquaient la cémentation pour durcir le fer et obtenir ainsi de l'acier.
Le latin adopte aussi l'hellénisme chalyb[5] pour désigner l'acier, le mot sideros n'étant utilisé que marginalement. Le terme général ferrum, d'origine sémitique (cfr. phénicien barzel, assyrien parzillu)[6], désigne le fer par opposition aux autres métaux, quelle que soit sa résistance ou son utilisation. C'est ce mot qui sera conservé dans les langues romanes (ferro en italien, fèrre en occitan, hierro en espagnol, fier en roumain).
Le Moyen Âge
[modifier | modifier le code]De manière globale, le terme « acier » désigne les alliages qui prennent la trempe, c'est-à-dire qui durcissent lorsque l'on trempe dans l'eau le métal chauffé au rouge. Le terme de « fer » désigne le métal qui ne durcit pas par trempe. Cette acception reste de nos jours dans les expressions « fer forgé » ou bien « fer plat », « fer U » et « fer I » qui sont des pièces en acier — au sens moderne du terme — ne prenant pas la trempe.
Réaumur, Monge, Berthollet et Vandermonde
[modifier | modifier le code]
Vers 1720, Réaumur étudie, en appliquant des règles scientifiques et même industrielles (calcul de prix de revient), les méthodes de fabrication du fer. Il affirme contre l'esprit commun de l'époque que « l'acier est un fer moins affiné où les molécules de fer sont séparées par des masses de soufre et de sels qui lui donnent sa dureté »[7]. Mais il faut attendre l'extrême fin du XVIIIe siècle pour que la distinction entre « fer », « acier » et « fonte » se fonde sur le taux de carbone contenu dans l'alliage.
Pendant la Révolution française, comme beaucoup de scientifiques, Monge, Berthollet et Vandermonde se mettent au service de la République. La France en guerre a besoin d'acier pour fabriquer des armes. Pour stimuler l'industrie nationale, très dépendante des importations de métal, ils synthétisent les connaissances et les pratiques de l'époque dans l'Avis aux ouvriers français en fer sur la fabrication de l'acier[MBV 1]. Dès le début, les auteurs établissent clairement la distinction entre fer, acier et fonte, en se fondant sur le taux de carbone :
« Le charbon n'a pas seulement la propriété d'ôter au fer l'air qui s'était uni à lui ; mais lui-même peut se fondre dans le fer à une grande chaleur, et par là, il donne des propriétés à la fonte et il change le fer en acier[MBV 2]. »
Cependant, quelques erreurs subsistent sur le rôle de l'oxygène, et on ignore à l'époque l'influence des autres éléments, comme le silicium. En effet, le texte continue ainsi :
« La fonte doit être considérée comme un métal dont la réduction n'est pas complète […]. Ainsi la fonte blanche retient une plus grande quantité d'oxygène et contient peu de charbon ; la fonte grise, au contraire, contient plus de cette dernière substance mais elle est beaucoup plus dépouillée d'oxygène[MBV 2]. »
Dans son ouvrage Description de l'art de fabriquer des canons, Monge rappelle que l'acier est « du fer affiné qui a absorbé du charbon, et c'est principalement par la quantité dont le charbon est distribué dans la masse que les aciers diffèrent entre eux »[8]. Le pluriel apparaît : si la définition de l'acier reste fondée sur sa teneur en carbone, il reste encore à expliquer la variété des propriétés de cet alliage.
Définition actuelle
[modifier | modifier le code]
Les alliages ferreux sont composés majoritairement de l'élément chimique fer. La distinction entre les trois familles d'alliages ferreux est fondée sur le taux de carbone contenu dans l'alliage, et en particulier sur la présence d'une phase eutectoïde ou eutectique :
- fer industriel et acier extra-doux : < 0,050 % de carbone ;
- acier[note 1] : entre 0,050 % et 2,1 % de carbone : présence d'une phase eutectoïde ;
- fonte : entre 2,1 % et 6,67 % de carbone : présence d'une phase eutectique[9].
Dans le cas du fer industriel, le carbone est entièrement dissous. Dans les aciers, une partie est sous la forme de précipités de carbures. Dans le cas des fontes, on peut avoir des précipités de carbure ou de graphite.
La définition par le taux de carbone est assez théorique, elle est établie pour un alliage purement binaire fer-carbone sans autre élément d'alliage. C'est une situation exceptionnelle qui ne tient compte ni des impuretés ni d'éventuels éléments d'alliages ajoutés volontairement.
Protohistoire : apparition de la métallurgie du fer
[modifier | modifier le code]L'âge du fer débute entre le IIe et le Ier millénaire av. J.-C., mais on ne sait encore que peu de chose sur sa genèse. Le consensus actuel, qui attribue aux Indo-Européens[10] parmi eux les Hittites l'invention de la production de fer et d'acier[11], s'appuie essentiellement sur la découverte d'objets en fer en Anatolie et contemporains à leur culture[note 2] : c'est avec eux que le fer commence à se substituer au cuivre et au bronze dans la fabrication des armes (lance, épée, poignard, hache). Ainsi, un des objets en fer non météoritique parmi les plus anciens jamais trouvés est une lame de dague, trouvée dans une tombe hattie, datée de -2500[12]. Cependant, la métallurgie du fer a peut-être été inventée indépendamment en Afrique subsaharienne[13],[14]. La question de savoir si la métallurgie africaine a été inventée indépendamment de celle du reste du monde n'est pas tranchée par la communauté scientifique[15].
De -2000 à -1600 (l'âge du bronze moyen au Proche-Orient), seul un nombre très restreint d'objets en fer nous est parvenu : quatre ont été trouvés en Asie Mineure, un en Crète et deux à Chypre. Mais les premières traces écrites évoquant la production de fer apparaissent à cette époque. Les écrits trouvés à Kültepe, Alalakh et Mari suggèrent que le fer était produit en Anatolie orientale depuis la fin du IIIe millénaire av. J.-C. et que le métal était alors précieux, sa disponibilité comme sa qualité restant très aléatoire[16].
À partir de -1500, les objets en fer non météoritique deviennent de plus en plus présents dans l'Est du bassin méditerranéen, mais ils demeurent rares : le bronze apparaît comme étant, de loin, le métal le plus employé[17]. C'est vers le XIIe siècle que le fer devient un métal plus courant, dans une zone allant de l'Afrique subsaharienne à l'Inde. Du fait, soit de problèmes d'approvisionnement en cuivre ou en étain[18], soit, plus probablement, de la diffusion de la technologie de réduction du minerai de fer[19],[18], l'âge du fer succède alors à celui du bronze au Levant, à Chypre, en Grèce, en Crète, en Égypte et en Anatolie[17]. L'origine de la dague de fer trouvée dans la tombe de Toutânkhamon a longtemps été sujette à débat, mais ses teneurs en nickel et en cobalt mesurées en 2016 ont montré qu'il s'agissait de fer météorique.
Époque | Fer | Argent |
---|---|---|
XIXe – XVIIIe siècles av. J.-C.[20] | 1 | 40 |
XIVe siècle av. J.-C.[21] | 12 | 23 |
VIIe siècle av. J.-C.[22] | 2 000 | 1 |
Si l'on en croit un texte akkadien du XIXe siècle avant notre ère trouvé à Kültepe, le fer coûtait alors huit fois plus cher que l'or[20]. Au XIVe siècle av. J.-C., un document comptable précise que 23 sicles d'argent sont équivalents à 12 sicles de fer[21]. Au VIIe siècle avant notre ère, en Grèce, 1 g d’argent ne coûte plus que le prix de 2 kg de fer[22]. Le fer est alors devenu un matériau utilitaire, et les armes fabriquées à base de fer se multiplient : une découverte importante de cette époque est un stock de Sargon II de 160 tonnes de fer à Dur-Sharrukin, avec tout un ensemble d'objets, dont des loupes forgées, des outils et des armes[19].
Peu de sites de production de fer ont été par contre découverts. Malgré des découvertes de laitier sur certains sites archéologiques du IIe millénaire av. J.-C., Jane Waldbaum constatait qu'en 1978, « on n'a encore trouvé aucune trace d'extraction de minerai, de fusion ou de travail du fer datant du début de l'âge du fer[17] ». En 1998, le constat était le même[19], les plus anciens bas fourneaux actuellement connus, à Tell Hammeh en Jordanie, n'ayant été datés que de -930[16]. Mais même sur ce site, où de nombreuses tuyères ont été retrouvées avec une grande quantité de laitier, « les traces de fourneaux restent très discutables[23] ». De fait, la connaissance actuelle des procédés primitifs est essentiellement issue de reconstitutions de bas fourneaux :
« [L'acier] est en fait d'abord une masse de métal impur. Dans un trou à même le sol, paré de pierres qu'ils recouvraient de couches d'argile, [les Hittites et les Chalybes] mettaient du charbon de bois qu'ils allumaient et sur lequel on entassait en couches alternées du minerai de fer et du charbon de bois. Ce minerai, ou oxyde de fer, se présentait alors sous la forme de petites roches que l'on ramassait à fleur de terre. La température que l'on obtenait dans ces trous était relativement basse, du fait d'un manque de soufflage efficace. Celui-ci provenait de tiges creuses au travers desquelles on soufflait. Ils obtenaient de ce fait et après bien des efforts, une masse pâteuse, incandescente, appelée loupe, qu'ils devaient impérativement battre énergiquement afin de la débarrasser de ses scories (résidus, dus à la chauffe et au charbon de bois). Ces « loupes », ensuite forgées sur un « tas » devenaient des objets de la vie quotidienne et aussi des armes[24]. »
Antiquité et Moyen Âge : l'acier « artisanal »
[modifier | modifier le code]Chine
[modifier | modifier le code]Production de fer, ses transformations en fonte ou en acier
[modifier | modifier le code]C'est pendant la période des Printemps et Automnes (771 à 453 av. J.-C.), bien que le bronze reste le métal dominant[25], que le fer, issu d'une loupe obtenue au bas fourneau, apparait et supplante progressivement le fer météorique[26].
La Chine est riche en minerai de fer, et l'argile utilisée s'avère être un excellent matériau réfractaire. Avec la mise au point de puissants soufflets, les artisans de l'époque y disposent des techniques nécessaires à la maîtrise de la fusion du fer[SF 1]. Il est alors fondu dans des fours de fusion au rôle semblable au cubilot[note 3],[27],[26]. Mais lorsque le fer chaud entre au contact avec le charbon de bois, il absorbe le carbone contenu dans le combustible jusqu'à s'en saturer. On obtient alors de la fonte, plus facile à fondre que le fer[note 4], homogène et débarrassée des impuretés présentes dans la loupe.
Les objets en fonte moulée apparaissent donc très tôt en Chine, peu après le fer[note 3], dès Ve siècle av. J.-C.[26]. La fonte se généralise pendant la période des Royaumes combattants (500 à 221 av. J.-C.)[28], au cours de laquelle les outils agricoles et les armes en fonte deviennent très répandus, tandis que les fondeurs du IIIe siècle av. J.-C. emploient des équipes de plus de deux cents hommes[29]. En effet, les Chinois comprennent très tôt, 20 siècles avant les Européens, les qualités de ce matériau et développent l'art de la fonderie, produisant des objets complexes et de qualité (comme des socs de charrue). À partir du IIIe siècle, la fonte blanche, cassante, est convertie, par un long recuit d'une semaine, en fonte malléable[30].

Même si la fonte moulée se généralise, la transformation de la fonte en fer ou en acier est connue. La « méthode des cent affinages » se développe au IIe siècle av. J.-C.[32]. Soigneusement décrite vers 120 av. J.-C.[SF 1], elle consiste à souffler alternativement, par deux soufflets, de l'air sur de la fonte martelée et chauffée au rouge[32]. Bien conduite, la méthode permet d'adapter la teneur en carbone à la zone de la pièce : le tranchant des épées est en acier dur alors que le dos de la lame est en fer[SF 1]. On met aussi au point au Ve siècle la fabrication de l'acier en mélangeant du fer avec de la fonte. Cette méthode, la cofusion de fer et de fonte, impose l'utilisation d'une fonte très pure[note 6], exempte d'éléments nuisibles (silicium, phosphore, manganèse, etc.)[SF 2]. Elle devient courante au VIe siècle[32].
Ces deux procédés, ainsi que leurs nombreuses variantes[33], que Joseph Needham corrèle aux procédés Bessemer et Martin-Siemens[32], n'évoluent pas vers une industrie sidérurgique, telle que l'Occident moderne l'inventera[SF 1]. À l'inverse, sous la dynastie Han apparait une méthode artisanale mais efficace, l'affinage chǎo (炒) (littéralement « saisir dans la poêle »)[34]. La technique se développe alors, l'industrie du fer est même nationalisée[SF 1] en 119 av. J.-C.[35].
Après l'invention du chǎo, d'autres procédés sont mis au point. Les Chinois importent le wootz d'Inde, et apprennent progressivement, pendant la dynastie Tang (618-907) à élaborer des aciers au creuset. Au XVIIe siècle (dynastie Ming), Song Yingxing décrit un procédé d'affinage de la fonte en fusion fondé sur le brassage de fonte en fusion avec une terre oxydante (peut-être du salpêtre)[31]. À la fin de la Dynastie Qing (1644-1912), l'affinage su gang est mis au point : il consiste à fondre une fonte dans une atmosphère oxydante, puis à la mélanger avec du fer[33].
Pour autant, la méthode chǎo se généralise. Elle consiste à mélanger des morceaux de fonte avec du charbon de bois en combustion. La combustion est attisée par une injection d'air dans le foyer, dont la conception (généralement un trou dans le sol surmonté d'une coupole) permet de limiter les pertes thermiques. Cette méthode et ses nombreuses variantes, parfois tardives (comme le chaolu du Sichuan, qui est décrit en 1905 comme un procédé de puddlage[36]), survivra jusqu'au milieu du XXe siècle.
Ces procédés d'affinage bénéficient d'innovations techniques importantes. Le livre d'agriculture de Wang Zhen illustre en 1313 l'utilisation de martinets hydrauliques. Ceux-ci servent à piler des céréales[37] mais, en 1637, Song Yingxing montre que l'usage y est généralisé dans les travaux métallurgiques, car le moulin à eau qu'il décrit actionne plusieurs martinets par alternance[38].
Invention du haut fourneau
[modifier | modifier le code]
Depuis environ 1000 av. J.-C., les Chinois connaissaient le fourneau attisé par un vent (gāo lú, 高爐), qui permet d'atteindre des températures élevées, mais ne l'utilisaient que pour la poterie[28].
En 31, le Chinois Du shi améliore la ventilation avec l'utilisation de la force hydraulique pour actionner le soufflet[39]. L'air de combustion peut alors traverser une charge plus haute et les fours de cette époque atteignent alors des dimensions imposantes : des restes d'un creuset ovale de 2,8 m × 4 m posé sur un socle de terre de 12 m × 18 m, avec des vestiges d'installations périphériques (rigole, mécanisme de hissage du minerai, soufflets...) ont été trouvés[40]. Cet accroissement de taille contribue à l'atteinte d'une température plus importante. Le four, alimenté énergiquement, devient capable de réaliser à la fois la réduction du minerai et la fusion du métal : le haut fourneau devient alors l'outil idéal pour la production de fonte.
Un additif, une « terre noire » contenant du phosphore (peut-être la vivianite[32]), est utilisé pour abaisser le point de fusion[note 7] : le métal liquide aide alors l'évacuation des scories (laitier). Cette technique disparaît avant le VIe siècle, lorsque l'amélioration des hauts fourneaux permet de s'en passer[SF 3].
Ainsi, mille ans avant l'Europe de la Renaissance, les Chinois maîtrisent parfaitement la production d'une fonte de qualité, ainsi que sa mise en œuvre. À l'inverse de l'Europe, qui se focalise sur la qualité de l'acier, la Chine va développer la production de grandes quantités de fonte, que les hauts fourneaux produisent directement à partir du minerai[SF 1].
Mais la production d'acier reste marquée par les contraintes locales. Dans le nord de la Chine, la pénurie du charbon de bois amène, avant le IVe siècle, à la mise au point de procédés utilisant la houille comme combustible et agent réducteur. Or il faut éviter tout contact entre le soufre, élément fragilisant apporté par le charbon, et le fer. Les Chinois mettent alors au point un procédé consistant à placer le minerai de fer dans des batteries de creusets tubulaires allongés et de recouvrir celles-ci d'une masse de charbon que l'on fait brûler[30],[SF 1]. Ce procédé, qui préfigure les procédés modernes de réduction directe en cornue a survécu jusqu'au XXe siècle[33]. Intégré à l'espace technique chinois, le Japon importe le bas fourneau (appelé tatara) du continent vers le VIIIe siècle pour la production du tamahagane, mais le four n'évolue pas en hauteur (donc vers le haut fourneau) du fait de la faible perméabilité des sables ferrugineux utilisés[41].
De l'Inde au monde islamique
[modifier | modifier le code]Aux alentours de l'an 300 av. J.-C. naît, dans la partie sud du sous-continent indien incluant le Sri Lanka, une technique de carburation du fer permettant de fabriquer de l'acier. Les lingots d'acier obtenus, connus sous le nom kannada de ukku « supérieur » en Inde du Sud (d'où wootz en anglais), sont élaborés en deux étapes :
- la réduction, par chauffage du minerai de fer à 1 200 °C avec du charbon de bois, du bois et des feuilles[42].
- la carburation, obtenue en chauffant le fer avec du carbone (charbon de bois probablement) à 1 200 °C dans un creuset hermétiquement fermé.
Le forgeage à basse température (rouge sang / cerise) rompt, sans le faire disparaître, le maillage de cémentite présent dans le lingot et permet de réduire l'hétérogénéité du lingot[43]. En plus de bonnes qualités mécaniques (dureté et souplesse), l'acier poli révèle de beaux dessins. La technique se répand de l'Inde à Merv, chef-lieu parthe sur la route de la soie, où le wootz était connu sous le nom de pōlāwad, d'où pûlâd en persan et fûlâh[43] en arabe. Ensuite, elle parcourt la Chine (bin tiě[note 8]) et la Mongolie (bolot) pour atteindre la Russie où le wootz se dit bulatʹ[44],[45].
C'est aussi à cette époque qu'est érigé le pilier de fer de Delhi, construit par soudure de lingots de fer brut. Sa teneur en phosphore, qui l'a protégé de la corrosion, donne un métal fragile[46]. La forge et les produits qui y sont utilisés (borax, chaux…) demeurent donc essentiels à l'obtention d'armes de qualité[43].
Le commerce avec l'Inde permet l'importation de lingots de wootz (acier à teneur en carbone de 1,5 à 2 %) en Iran, où les forgerons produisent le renommé acier de Damas sur une période s'étalant de 900 à 1750.
Bien que relativement pauvre en gisements de minerai de fer, le monde islamique est pionnier dans l'équipement de ses forges de moulins à eau et à vent. Les premières traces de pilon hydraulique sont localisées à Samarcande (973 ou avant) et dans la Perse médiévale, avant que la technique ne se diffuse dans tout le monde islamique. Cette mécanisation, qui se généralise de l'Asie centrale à l'Espagne islamique au cours du XIe siècle, se développe particulièrement durant le XIIe siècle en Espagne. Au XVIIe siècle, l'adoption de la trompe hydraulique permet l'éclosion de la forge catalane.
En Europe : le bas fourneau pour produire l'acier
[modifier | modifier le code]Antiquité : développement de la métallurgie du fer
[modifier | modifier le code]Le travail du fer est introduit en Grèce antique à la fin du Xe siècle av. J.-C.[47], en Europe centrale durant l'époque Hallstatt C[48] (VIIIe siècle av. J.-C.). Durant les VIIe et VIe siècles av. J.-C., ces objets en fer sont coûteux et réservés à une élite. Homère s'en fait l'écho dans l’Iliade où un disque de fer brut est offert au vainqueur d'une épreuve d'athlétisme[49]. Cette situation change brutalement peu après 500 av. J.-C. avec l'avènement de la Tène[50] ; la métallurgie du fer se répand en Europe du Nord et dans les îles Britanniques. La diffusion dans l'Europe centrale et de l'Ouest est associée à l'expansion celte.
La compétition entre l'utilisation du bronze et celle du fer, notamment pour les épées, dure plusieurs siècles. Les Romains, qui disposent du cuivre espagnol, ne voient l'intérêt de changer pour des épées en fer qu'au moment des guerres puniques[51]. Au Ier siècle av. J.-C., les Romains, qui diffusent leurs pratiques de la métallurgie du fer dans leur empire[F 1], apprécient particulièrement la qualité de l'acier norique[52]. La production annuelle de fer de l'Empire romain est alors estimée à 54 750 tonnes[53] alors qu'à la même époque, la Chine des Han, qui est pareillement peuplée, ne produit que 5 000 tonnes annuelles[54].
Moyen Âge : apparition d'une industrie
[modifier | modifier le code]
Cette reconstitution évoque la présence, en 1220, d'un des premiers martinets européens.
L'adoption massive du fer stimule alors le perfectionnement des procédés : les fourneaux des Romains s'agrandissent à partir du IIe siècle av. J.-C.[SF 4]. Alors qu'ils ne produisaient guère que 4 à 5 kg de fer par opération, cette quantité atteint 50 à 60 kg au Moyen Âge, la limitation venant essentiellement des difficultés d'approvisionnement en matières[F 2].
Le développement de l'ordre cistercien est le principal facteur expliquant l'expansion de la production européenne de fer à partir du XIe siècle[55]. Étudiant et propageant les meilleures technologies métallurgiques, les cisterciens propulsent la métallurgie européenne à un haut niveau : en France et en Angleterre, l'efficacité de leurs « fours à masse » se révèle très proche de celle d'un haut fourneau[56],[57]. Au début du XIIIe siècle, les fours à masse sont d'imposants bas fourneaux construits en pierre pour être durables : l'extraction de la loupe se fait par une grande ouverture à la base du four. Un exemple abouti de ce type de four, caractéristique de l'espace germanique, est le stückofen[58], de section carrée et maçonné, qui s'élève à 4 m[59],[SF 5]. Le laitier doit être évacué régulièrement du four afin de permettre au vent d'oxyder le carbone du charbon de bois, qui est inévitablement absorbé par le métal. Dans le cas contraire, le métal, trop riche en carbone, est insuffisamment malléable ; il peut même n'être qu'une fonte extraite à l'état solide du four. La maîtrise du laitier, qui doit dorénavant être fusible, est une contrainte caractéristique de l'exploitation des fours à masse[60].
Les fours, de plus en plus gros, produisent des loupes d'une telle dimension qu'il n'est plus possible de les travailler à la main[61]. Au XIIe siècle apparaît en France l'usage de l'énergie hydraulique pour actionner des martinets : une première source mentionne leur usage en 1135 à l'abbaye de Clairvaux, point de départ d'une diffusion rapide et bien documentée dans toute l'Europe[SF 6],[62]. Ces outils démultiplient la capacité de production des forgerons : l'utilisation de martinets permet de travailler des pièces plus imposantes (les marteaux de l'époque pouvaient peser 300 kg et frapper 120 coups à la minute[Gi 1]) et plus rapidement (des marteaux de 80 kg frappant 200 coups à la minute[Gi 1]).

De même, l'augmentation de la puissance de la soufflerie est nécessaire à cause de la hauteur du four : l'air doit être insufflé à 0,7 bar pour pouvoir traverser la charge. S'il est encore possible d'utiliser des soufflets, ceux-ci doivent être actionnés avec des roues hydrauliques[60]. La force hydraulique se prête aussi bien à la mise en œuvre des marteaux que des soufflets, mais il semble que le martelage hydraulique a précédé les souffleries[55] : la première application est attestée dès le XIIe siècle, la seconde n'est évoquée qu'à partir du XIIIe siècle[SF 7].
Ainsi, l'adoption de l’énergie hydraulique se produit en Europe douze siècles après les Chinois[SF 7]. L’utilisation de cette énergie, tout comme la taille croissante des fours, fait des forges des usines sédentaires. Le bas fourneau, qui a été pendant tout le Moyen Âge un procédé nomade qu'on édifie en fonction des affleurements de minerai et de la disponibilité du combustible[F 3], amorce son évolution vers l'industrie sidérurgique[SF 6],[SF 7].
Cette industrie, qui bénéficie alors de l'amélioration du transport des matières, reste très contrainte par ses besoins en bois et par la disponibilité de l'énergie hydraulique. La consommation de combustible est considérable : pour obtenir 50 kg de fer par jour, il faut quotidiennement 200 kg de minerai et 25 stères de bois ; en quarante jours, une seule charbonnière déboise une forêt sur un rayon de 1 km[Gi 2],[F 3]. Ceci ne pose pas de problème tant que les défrichages sont utiles au développement de l'agriculture, mais au XIIIe siècle une limite est atteinte : les forêts gardent un rôle nourricier important, le bois est indispensable à la construction comme au chauffage[63],[64]. La noblesse, qui tire des revenus de l'exploitation forestière, doit réglementer progressivement la coupe du bois[63]. Ainsi, au XIIIe siècle, quand le roi d'Angleterre fait faire le compte pour sa grande forge dans la forêt de Dean, il constate que vendre le bois consumé par cette forge lui rapporterait plus que la forge même[55].
XVe siècle en Europe : adoption du procédé indirect
[modifier | modifier le code]Apparition du haut fourneau
[modifier | modifier le code]Une réinvention européenne tardive
[modifier | modifier le code]L'utilisation de l'énergie hydraulique attise significativement la combustion dans le four. Les forges à bras, nombreuses encore au XVIe siècle, sont progressivement remplacées par des forges hydrauliques se concentrant au bord des rivières qui sont l'objet d'un phénomène d'appropriation privée par les seigneurs laïcs et ecclésiastiques. Ce processus voit le développement des soufflets hydrauliques qui remplacent les soufflets à main et qui permettent d'obtenir des températures plus élevées dans des fours de plus grande taille. Parallèlement, le développement de martinets permet de mettre en forme les barres utilisées dans l'architecture gothique (tirants, barlotières) et l'artillerie à poudre (bombardes non plus en fer forgé et fretté, mais coulées en fonte, dans des moules), objets en fer dont la quantité et la dimension imposent l'emploi de ces soufflets et marteaux hydrauliques[65].
L'élévation de température (à plus de 1 200 °C à l'intérieur d'un bas fourneau[Gi 1]) s'accompagne d'une diffusion plus rapide du carbone provenant du charbon de bois dans le métal. Il en résulte que celui-ci contient des teneurs plus élevées en carbone que l'acier, ce qui abaisse sa température de fusion. Or avec l'augmentation de leur taille, les températures au cœur du four montent encore, jusqu'à atteindre 1 600 °C. L'influence conjuguée d'un foyer plus chaud avec une matière devenue plus fusible permet au métal de sortir à l'état liquide du fourneau[L 1],[SF 8]. Ce four produisant de la fonte en fusion ne peut plus être qualifié de four à loupe, mais il prendra plusieurs appellations avant de devenir le « haut fourneau », au sens moderne du mot[66].
![]() |
![]() | |
Photo et schéma des vestiges du haut fourneau de Lapphyttan, opérationnel entre 1150 et 1350.
|
Cette évolution, du bas fourneau vers un four à masse si élaboré qu'il peut produire de la fonte en fusion, se produit en Europe en divers endroits, du XIIe au XVe siècle[SF 9]. Le lieu et la date précise d'apparition des premiers hauts fourneaux ne sont pas encore établis avec certitude : les plus anciens hauts fourneaux européens attestés sont des vestiges de Lapphyttan, en Suède, où le complexe a été actif de 1150 à 1350[67],[68],[69]. À Noraskog, dans la paroisse suédoise de Järnboås, on a aussi trouvé des traces de hauts fourneaux encore plus anciens, datant peut-être de 1100[70]. En Europe continentale, des fouilles ont mis au jour des hauts fourneaux en Suisse, dans la vallée de Dürstel, près de Langenbruck, et datés entre les XIe et XIIIe siècles[71]. On a aussi identifié en Allemagne un four produisant de la fonte en fusion (un Flussofen) dans la vallée de la Kerspe daté de 1275[72] et, dans le Sauerland, des hauts fourneaux datés du XIIIe siècle[73]. Tous ces hauts fourneaux primitifs sont techniquement proches des bas fourneaux : édifiés en argile avec des pierres, leurs vestiges ne dépassent pas 2 m de haut[SF 9].
Une transmission de la technologie de la Chine vers l'Europe est envisageable mais n'a jamais été démontrée. Au XIIIe siècle, Al-Qazwini note la présence d'une industrie du fer dans les monts Elbourz au sud de la mer Caspienne, dont les techniques auraient pu arriver par la route de la soie[74]. Cette technologie aurait pu alors rayonner vers l'Europe, vers la Suède, suivant la route commerciale des Varègues (Rus') le long de la Volga, ou vers le Nord de l'Italie où, en 1463, Le Filarète décrit un procédé en deux temps à Ferriere[74], avec un haut fourneau dont la fonte était coulée deux fois par jour dans de l'eau pour en faire un granulé[75].
Ainsi, il est plus probable que le haut fourneau européen soit apparu en Scandinavie et ailleurs, indépendamment des inventions chinoises[68]. La fonte issue du haut fourneau, appelée à l'époque « fer coulé » (cette appellation perdurera et sera encore utilisée par Monge à la fin du XVIIIe siècle)[76], est facilement moulable. Mais les européens mettront du temps pour en développer la métallurgie et les usages. En effet, contrairement aux Chinois, si « les Européens ont fait de la fonte en Suède vers le XIIIe siècle, ils ne l'ont pas employée pour faire des moulages. Nous n'avons ni pots, ni poêles (pour la cuisson), ni cloches, ni plaques de foyer datant de cette époque[68]. »
C'est au XVe siècle que s'amorce la généralisation du haut fourneau en Europe, à Namur (Wallonie), grâce à la mise au point d'un procédé efficace d'affinage de la fonte, la « méthode wallonne », qui permet la production massive d'acier naturel[58]. De là, les hauts fourneaux se répandent en France, dans le pays de Bray (Normandie), puis en Angleterre, dans le Weald (Sussex)[77].
Une généralisation ralentie par la pénurie des ressources
[modifier | modifier le code]La production européenne de fer forgé est estimée entre 25 000 et 30 000 tonnes annuelles vers 1400. Elle atteint environ 40 000 tonnes vers 1500. Mais cette progression ne peut pas être attribuée à la généralisation du haut fourneau et des procédés d'affinage. En effet, si la technologie se diffuse rapidement, son adoption n'est pas systématique. Elle a d'abord l'inconvénient d'être gourmande en combustible : le coût du charbon de bois, qui représente de 30 à 50 % des frais d'une renardière nomade, monte jusqu'à 72 % avec le procédé indirect. Celui-ci exacerbe ainsi les tensions sur le bois[55] :
« Ce procédé a l'avantage d'accélérer considérablement la production malgré les deux phases successives qu'il rend nécessaires, et il garantit en même temps une plus grande productivité en permettant de restreindre le personnel. D'autre part, il a le désavantage d'entraîner une très grosse consommation du bois à brûler comparée à une unité de fer produit. […]
Il est évident que le procédé indirect rendait possible une augmentation de la productivité qui équilibrait en partie l'accroissement des frais en bois. Toutefois, si le personnel était très nombreux, l'application du procédé indirect n'était presque jamais rentable[55]. »
— Rolf Sprandel, La production du fer au Moyen Âge
La pénurie peut également concerner le minerai. Au XVe siècle, il représente ainsi 45 % des coûts des forges liguriennes, 40 % aux fourneaux de l'Erzberg[55]. L'industrie minière se développe avec la mise au point de techniques d'étayage ou de drainage des galeries inondées[Gi 3]. L'usage des explosifs apparaît dès le XVIe siècle et permet de descendre jusqu'à 20 mètres au-dessous de la surface[F 4].
Pareillement, la disponibilité de l'énergie hydraulique est essentielle et dicte l'emplacement de l'atelier. La capacité à fonctionner toute l'année dépend d'aménagements hydrauliques :
« L'eau est pour les forges une puissance nécessaire dont on ne tire pas tout l'avantage possible sans beaucoup d'intelligence, de travail et de dépenses. Il n'est pas nécessaire de dire qu'il ne faut pas entreprendre la construction d'une forge, si, par le calcul fait d'avance, il est clair qu'on ne puisse ramasser assez d'eau et à telle hauteur[78]. »
Avec la mise au point de méthodes d'affinage de la fonte (méthodes wallonne, champenoise, osmond, etc.), l'activité devient ainsi de plus en plus capitalistique. En 1671, les bas fourneaux de Putanges, en Normandie, sont vendus en bloc pour 500 livres, pour être remplacés par un haut fourneau loué 1 200 livres par an[F 5]. Toutes ces contraintes expliquent la survivance de bas fourneaux perfectionnés, comme la forge catalane qui, en France, ne disparaît qu'au début du XIXe siècle, lorsque le procédé Thomas se généralise[G 1],[79].
L'acier naturel
[modifier | modifier le code]L'affinage de la fonte est réalisé par des méthodes empiriques qui permettent d'éliminer le carbone des gueuses de fonte provenant des hauts fourneaux. Les différentes méthodes sont à l'origine régionales et correspondent probablement en partie aux qualités des minerais de fer utilisés. La méthode la plus répandue est la méthode dite « wallonne ». Cette méthode a été utilisée dans une grande part de l'Europe jusqu'au XVIIe siècle. Il en existe des variantes comme la méthode champenoise ou la méthode comtoise[80] dans laquelle la gueuse est placée au milieu du foyer et non au-dessus. Il existe cependant des méthodes présentant des différences importantes comme la « méthode nivernaise ».
La méthode wallonne
[modifier | modifier le code]La gueuse de fonte est poussée sur les flammes d'un foyer ventilé par des soufflets. Sous l'effet de la chaleur, le carbone contenu dans la fonte s'oxyde en brûlant. Les gouttes de fer tombent dans le caisson contenant le foyer. Ce dernier est refroidi par le dessous afin de permettre la solidification de la loupe de fer[81]. Un ouvrier aide le processus en piquant l'extrémité molle de la gueuse à l'aide d'un « ringard à piquer ».
Ce procédé présente plusieurs inconvénients : la loupe se charge de scories dans le foyer et la température n'est pas suffisante pour oxyder le phosphore (En savoir plus), de sorte qu'il n'est possible d'utiliser que des fontes blanches car pauvres en phosphore.
Comme pour les loupes de fer obtenues au bas fourneau, les scories sont éliminées par « cinglage ». Cette opération de forge est réalisée à l'aide d'un martinet en frappant énergiquement la loupe à coups vifs et répétés.
La méthode nivernaise
[modifier | modifier le code]La fonte est fondue (ou semble-t-il fortement ramollie) dans un four appelé « mazerie » avec du charbon de bois et des scories. Cette fonte est ensuite coulée sur un revêtement réfractaire refroidi par de l'eau. L'affinage est effectué en faisant passer de l'air sur l'ensemble.
En 1786, le baron Philippe-Frédéric de Dietrich décrit ainsi cette méthode[82] :
« Le travail de la mazerie est principalement en vigueur dans le Nivernois, et c'est un commis de cette province qui l'a mis en usage à la forge d'Uza. Il est trop peu connu ailleurs. J'ai eu l'occasion de voir ce travail en assez grand détail dans les forges royales du Nivernois, ce qui met à porter d'en donner une idée.
Il consiste en trois procédés distincts : 1°. dans la refonte complète de la gueuse, pour la convertir en gâteaux : 2°. dans le grillage de ces gâteaux : 3°. dans leur affinage.
En quelques endroits on maze la gueuse, et on affine les gâteaux dans le même feu ; en d'autres on a un feu destiné à la fusion, et un autre à l'affinage.
Le feu de fusion porte le nom de mazerie.Ses dimensions sont de seize à dix-huit pouces de profondeur ; ses côtés en ont seize à dix-huit en tous sens, du sol à leurs bords : le fond du creuset est incliné vers le chio qui se trouve au ras du sol.
La tuyère entre dans l'aire, en affleurant les bords du feu, et on lui donne plus ou moins de saut, suivant la qualité de la fonte : si elle est douce on la relève ; si elle est dure & âcre, on l'incline davantage ; en la relevant, elle porte plus immédiatement sur la gueuse, et moins sur la matière fondue.
La gueuse se place au contre-vent par son extrémité. On l'environne et la recouvre de laitier de grosses forges, et on la charge en même temps des calottes de fordes ou avec un ringard : cette opération exige fort peu de travail ; on obtient en peu de temps une petite pièce qui porte le nom de maffiot, du poids de quarante et quelques livres. »
Cette méthode persistera. Elle est ainsi décrite par Grüner et Lan en 1862[83] :
« … il suffira de rappeler rapidement les principes et les résultats […] du mazéage.
Cette manipulation s'exécute toujours, en Angleterre, dans les bas foyers de coke, connus sous le nom de finerie anglaise. Le travail, chacun le connaît : c'est la fusion de la fonte, seule ou additionnée de battiture ou de scorie de forges, sous l'influence d'un courant d'air. La position de la fonte par rapport aux tuyères, l'inclinaison du vent, sa pression, la profondeur du foyer, etc., etc., sont autant qui font varier l'intensité l'action de l'air sur le métal. »
L'acier de cémentation
[modifier | modifier le code]Les fers obtenus peuvent subir des opérations de cémentation. Cette opération, attestée dès l'Antiquité, consiste à augmenter le taux de carbone de la couche superficielle de l'alliage afin d'obtenir des caractéristiques mécaniques supérieures.
Quant au procédé moderne de cémentation dans des fours dédiés, il est attesté dès le XVIe siècle[84].
En France, Nicolas-Prosper Bauyn d'Angervilliers, intendant d'Alsace, communique à Réaumur une méthode employée en Allemagne pour la fabrication de l'acier au creuset. Réaumur conçoit en 1822 un four fait de plaques de réfractaire mobiles. Sur ces plaques, il place des barres de fer forgées noyées dans divers mélanges carbonés faits à base de bois pilé, de cendres et de suie. L'ensemble est chauffé pour provoquer une migration du carbone par diffusion dans les barres (phénomène de cémentation) : les barres de fer chauffées au rouge sont alors corroyées, c'est-à-dire soudées et forgées[85].
Si la fonte et le fer sont entrés dans l'ère industrielle, l'acier de cémentation reste un produit coûteux. Au début du XIXe siècle au Royaume-Uni, on l'obtient encore en chauffant du fer suédois en contact avec du charbon de bois, pendant 6 semaines[B 1]. Ses avantages sont connus et compensent son prix : en jouant à la fois sur la teneur en carbone et sur les traitements thermiques, il permet au métallurgiste d'obtenir un matériau dur, résistant ou ductile.
Production au haut fourneau et puddlage de la fonte
[modifier | modifier le code]XVIIIe et début du XIXe siècle : la métallurgie scientifique
[modifier | modifier le code]La connaissance scientifique de l'acier est indissociable du travail des savants du XVIIIe siècle : Réaumur, Gabriel Jars, Grignon, Guillot-Duhamel, Lavoisier et Hassenfratz, pour citer les principaux, qui inventent le terme « sidérurgie » pour exprimer la rationalisation de la production des métaux ferreux.
Gaspard Monge, Claude-Louis Berthollet et Alexandre-Théophile Vandermonde catégorisent en trois catégories les « aciers » en se basant sur leur méthode d'élaboration :
- L'acier naturel (ou acier d'Allemagne) : fabriqué par décarburation de feuillets de fonte.
- « Ces feuillets sont destinés à être convertis en fer ou en acier… est-ce de l'acier que l'on a l'intention de faire ? On emploie un fourneau d'affinerie plus étroit et plus profond, on le brasque avec de la charbonaille qu'on humecte… ensuite on y dispose les feuillets, et on les recouvre de scories et de charbon[MBV 3]… »
- L'acier de cémentation : fabriqué à partir de fer solide dans lequel on augmente le taux de carbone par diffusion.
- « On fait dans le fond de la caisse un lit de poussier de charbon… : on met sur ce lit un rang de bande de fer, que l'on place de façon que chaque bande puisse être environnée de poussier ; ensuite on recouvre totalement ce premier rang avec un lit d'un demi-pouce d'épaisseur de poussier de charbon : on continue ainsi successivement jusqu'à ce que le creuset soit plein : le dernier rang est recouvert de poussier de charbon, par-dessus lequel on met un lit de sable, pour couvrir entièrement sa surface, et empêcher qu'il soit détruit par la combustion… À Newcastle où l'on cémente dans deux caisses, contenues dans un fourneau, de 25 à 30 milliers d'acier, l'opération dure 5 jours et 5 nuits[MBV 4]. »
- L'acier fondu : c'est une méthode permettant d'améliorer la qualité de l'acier produite par une des deux méthodes précédentes. L'acier est fondu pour homogénéiser sa composition.
- « On met l'acier dans le creuset avec un flux, dont on fait un secret ; et l'on place le creuset sur une brique ronde, on pose sur la grille. On a du charbon de terre réduit en coak qu'on met autour du creuset, et on remplit le fourneau ; on y met le feu, et l'on ferme entièrement l'ouverture supérieure du fourneau, avec une porte faite de brique, entouré d'un cercle de fer.
Le creuset est cinq heures au fourneau, avant que l'acier soit parfaitement fondu[MBV 5]. »
- « On met l'acier dans le creuset avec un flux, dont on fait un secret ; et l'on place le creuset sur une brique ronde, on pose sur la grille. On a du charbon de terre réduit en coak qu'on met autour du creuset, et on remplit le fourneau ; on y met le feu, et l'on ferme entièrement l'ouverture supérieure du fourneau, avec une porte faite de brique, entouré d'un cercle de fer.
Le haut fourneau moderne
[modifier | modifier le code]L'histoire du haut fourneau est marquée par les innovations qui ont permis d'atteindre les hautes températures nécessaires à la fusion de la fonte et du laitier, qui facilite les réactions chimiques entre ces deux produits. Dans ce contexte, trois innovations sont généralement considérées comme essentielles[SF 10] :
- l'utilisation des énergies hydrauliques ou éoliennes pour le soufflage de l'air de combustion ; l'adoption de technologies développées pour d'autres usages se fait dès l'Antiquité, indépendamment du lieu ;
- le remplacement du bois par la houille au début du XVIIIe siècle ;
- le préchauffage de l'air de combustion vers le milieu du XIXe siècle.
1709, première coulée de fonte au coke
[modifier | modifier le code]Le charbon, comme combustible et agent réducteur, avait été adopté par les Chinois durant la période des Royaumes combattants au IVe siècle av. J.-C.[28]. Inconnu des Arabes, difficile d'extraction dans la quasi-totalité de l'Europe, ce combustible était resté assez méconnu des Européens. Bien que les Chinois aient mis au point un fourneau au charbon où ce combustible n'entrait pas en contact avec le fer[30], et que la houille était largement utilisée en complément du bois dans les forges au XVIIIe siècle, le remplacement du charbon de bois par cette roche dans un haut fourneau ne donnait que des fontes de mauvaise qualité[F 6].
En effet, la houille contient des éléments qui, faute de post-traitement approprié (le mazéage), modifient la qualité de la fonte. Le silicium, en limitant la solubilité du carbone dans le fer, va permettre la formation de lamelles de graphite, qui affaiblissent le métal[L 2]. C'est la fonte grise que les métallurgistes de la fin du XVIIIe siècle, qui se trompent sur sa composition, estiment comme la seule apte à se transformer en acier[MBV 6], mais déplorent sa difficile conversion en fer :
« [La fonte grise] a retenu moins d'oxygène, mais elle contient beaucoup plus de charbon ; elle est plus douce et préférable pour les usages pour lesquels on exige cette qualité ; mais elle est plus difficile à convertir en fer, parce que pour cela il faut détruire la plus grande partie du charbon qui, dans cet état, résiste considérablement à la combustion[MBV 2]. »
Le soufre est plus problématique. Connu dès le Moyen Âge et facilement décelable dans la combustion de la houille de par son odeur, il est un élément fragilisant et affaiblissant dès que sa teneur dépasse 0,08 %[SF 11]. Lorsqu'il se combine au manganèse, fréquent dans les minerais de fer, il dégrade considérablement les qualités des aciers[L 3]. Contrairement au silicium, l'extraction du soufre dissous dans la fonte liquide est difficile car il ne peut être consumé par de l'air.

C'est Abraham Darby, qui était torréfacteur à l'origine, qui réalise en 1709 la première coulée de fonte au coke[note 9], dans le petit haut fourneau de Coalbrookdale qu'il avait loué[86] :
« Il lui vint à l'esprit qu'il était envisageable de fondre le fer dans le haut fourneau avec du charbon de terre, et, de là, il tenta premièrement d'utiliser du charbon brut, mais cela ne marcha pas. Il ne se découragea pas, transforma le charbon en cendre, comme cela est fait avec le touraillage du malt, et obtint enfin satisfaction. Mais il découvrit qu'une seule sorte de charbon de terre était la mieux adaptée à la fabrication de fer de bonne qualité[86]… »
— T. S. Ashton, Iron and Steel in the Industrial Revolution
Le coke, plus résistant à l'écrasement que le charbon de bois, simplifie l'exploitation du haut fourneau. Mais l'utilisation de coke issu de charbons peu soufrés est un élément clé pour la qualité de la fonte. La fonte au coke, réputée de moins bonne qualité que celle au bois et impropre à la production d'acier, met 50 ans à s'imposer avant que ce point soit bien compris par les concurrents de Darby.
Communiquant très peu sur les détails du procédé[A 1], les Darby améliorent continuellement le procédé et la qualité de la fonte produite. Vers 1750, Abraham Darby II envoie ses gueuses de fonte à des forges sans en préciser le procédé d'obtention : la fonte au coke se révèle parfaitement apte à la conversion en fer « sans qu'aucun préjugé n'apparaisse tant qu'il n'avait pas révélé d'où les gueuses venaient et comment elles avaient été produites[86] ».

La production de fonte au charbon de bois persiste en raison de la qualité attribuée à ce type de fonte et des réticences de certains maîtres de forges, mais également à cause du protectionnisme pratiqué par les pays producteurs (France, Allemagne…) vis-à-vis de l'expansion de la sidérurgie britannique[F 7]. En 1760, le Royaume-Uni ne compte que 17 hauts fourneaux au coke mais 20 ans plus tard, le nouveau procédé s'y est généralisé : il ne se construit plus de haut fourneau au charbon de bois. S'affranchissant de la faible disponibilité du bois (également nécessaire à la construction navale), la production totale de fonte britannique va alors croître de manière exponentielle. En 1809, un siècle après l'invention de la fonte au coke, la production annuelle atteint 400 000 tonnes, alors que celle de fonte au charbon de bois oscille entre 15 000 et 25 000 tonnes sur cette même période. Après cette date, les hauts fourneaux au charbon de bois disparaissent du Royaume-Uni[87]. Autrement dit, le remplacement du charbon par le coke comme nouvelle matière première de production de l'acier n'est devenu dominant, dans ce pays, qu'au cours du dix-septième siècle[88].
En France, les premiers essais au coke n'ont lieu qu'en 1769 à Hayange avant que ne soient construits, sous la direction du Britannique William Wilkinson, les hauts fourneaux au coke du Creusot. Les guerres avec l'Angleterre suspendent ensuite tout développement[A 1]. La paix revenue, les maîtres de forges sont contraints d'adopter le procédé pour lutter contre les importations d'acier anglais. Mais ce nouveau procédé était lent et ne s'est généralisé dans l'hexagone que vers la fin du dix-neuvième siècle[88].
La sidérurgie américaine abandonne le charbon de bois à la même époque. Bien qu'ayant accès aux technologies anglaises, elle est moins contrainte par la disponibilité en bois. Elle bénéficie aussi de l'anthracite de Pennsylvanie, directement utilisable au haut fourneau, puis l'abandonne progressivement au profit du coke[90].
Au XIXe siècle, l'utilisation du coke permet un changement radical dans la technique. Outre la disponibilité de ce combustible, sa résistance à la compression à haute température permet de conserver une bonne perméabilité au gaz réducteur. La hauteur des hauts fourneaux atteint alors vingt mètres, ce qui améliore significativement le rendement thermique. L'augmentation de taille modifie aussi l'aspect du four : l'ancienne architecture pyramidale en maçonnerie est remplacée par une construction plus légère et plus solide en fer. Mieux refroidi, le revêtement réfractaire dure aussi plus longtemps[T 1].
Le préchauffage de l'air
[modifier | modifier le code]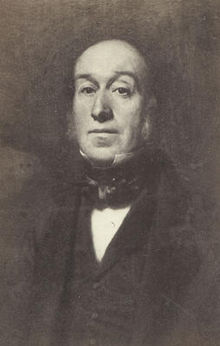
L'Écossais James Beaumont Neilson, spécialiste du traitement des gaz industriels et directeur de la Glasgow Gas-works, a effectué plusieurs recherches en vue d'améliorer le pouvoir éclairant du gaz de ville. Informé de l'importance que les maîtres de forges attribuent aux caractéristiques de l'air de combustion des hauts fourneaux, il leur expose une de ses découvertes : la combustion d'un gaz est plus vive avec de l'air chaud qu'avec de l'air froid. De cette observation, il leur propose de préchauffer également l'air de combustion de leurs hauts fourneaux pour améliorer leur marche[91].
Cette idée n'est pas nouvelle : un ingénieur nommé Seddeger l'a proposée en 1799 et un autre, Leichs, a fait des expériences dans ce sens de 1812 à 1822[92]. Pourtant, la proposition est encore accueillie avec un certain scepticisme :
« Sa théorie était en total désaccord avec la pratique établie, qui se privilégiait un air le plus froid possible, l'idée communément admise étant que la froideur de l'air en hiver expliquait la meilleure qualité de la fonte alors produite. À partir de ce constat, les efforts des maîtres de forges s'étaient toujours dirigés vers le rafraîchissement de l'air insufflé, et divers expédients avaient été inventés dans ce but. Ainsi les régulateurs étaient peints en blanc, on passait l'air sur de l'eau froide et dans quelques cas, les pipes d'injection avaient même été entourées de glace. Quand donc Neilson proposa d'inverser entièrement le process et d'employer de l'air chaud au lieu du froid, l'incrédulité des maîtres de forges est facilement imaginable[91]… »
— R. Chambers, Biographical Dictionary of Eminent Scotsmen
En effet, personne n'avait alors compris que l'avantage de l'air froid réside uniquement dans le fait qu'il est plus sec[93]!
Des premiers essais sont cependant entrepris et s'avèrent encourageants. Bien qu'aucun système de réchauffage de l'air satisfaisant ne puisse être mis au point, le principe est breveté en 1828. Pour encourager le développement d'un réchauffeur adapté, Neilson se contente d'une modeste royaltie d'un shilling par tonne produite avec son procédé[note 10]. En 1829, il réalise la première machine industrielle qui chauffe l'air à 150 °C, à Clyde. En 1931, Calder Works met en œuvre un air à environ 350 °C[92]. Même en tenant compte de la consommation de combustible du réchauffeur[L 4], de type tubulaire[G 2], la chaleur apportée permet une économie globale de charbon pouvant atteindre un tiers, tout en diminuant sensiblement la teneur en fer du laitier[94]. À l'inverse de l'usage du coke, qui avait mis presque un siècle à s'imposer, le procédé est rapidement adopté[note 11]. Son intérêt est démontré par les scientifiques qui énumèrent ses avantages :
« 1. Dans la partie basse du haut fourneau, le carbone n'est pas oxydé en CO2, mais seulement en CO. Brûler [une livre de lignite] dans le haut fourneau ne génère que 2 473 Btu alors que sa combustion complète, telle qu'elle se passe lorsqu'on chauffe le vent, génère 8 080 Btu […]
2. L'utilisation d'air chaud accélère la fusion des matières à proximité des tuyères.
3. Quand la température est suffisamment élevée, le carbone est brûlé directement en monoxyde de carbone et la chaleur est concentrée [aux tuyères]. Avec le vent froid, du dioxyde de carbone est produit près des tuyères, puis est décomposé en monoxyde plus haut dans le four, ce qui disperse la combustion[note 12].
4. Puisque la combustion est plus locale et qu'il faut moins d'air [pour brûler moins de coke], le haut du four est plus froid et moins de chaleur est emportée par les fumées.
5. Moins de coke implique moins de cendres à évacuer sous la forme de laitier, ce qui diminue la quantité de fondant nécessaire, et donc de combustible.
6. Puisque moins de coke est nécessaire, il faut moins de temps pour le brûler. Cette quantité de coke est, à volume de four donné, avantageusement remplacée par du minerai, ce qui dope la productivité du four[T 2]… »
— T. Turner, The metallurgy of iron
Malgré les évolutions ultérieures, l'allure générale du four a si peu changé qu'on l'appelle encore aujourd'hui cowper.
La chaleur nécessaire au réchauffage de l'air peut venir de combustibles bien meilleur marché que le coke : l'appareil de Neilson se contente de charbon de qualité médiocre[T 3]. Cependant, le pouvoir calorifique des fumées de haut fourneau, qui s'enflamment spontanément en sortant du gueulard, n'avait échappé à personne : dès 1814, le Français Aubertot les récupérait pour chauffer quelques fours annexes de son usine[T 4]. En effet, l'intérêt de ces fumées consiste en la présence d'une faible proportion (environ 20 % à l'époque) de monoxyde de carbone, un gaz toxique mais combustible[T 5].
En 1837, l'Allemand Faber du Faur met au point le premier réchauffeur d'air, tubulaire, prélevant les gaz avant que ceux-ci ne sortent de la charge[L 5],[note 13]. James Palmer Budd dépose un brevet similaire en 1845, mais en proposant une méthode pratique de captation des gaz : ceux-ci sont prélevés sous le gueulard et descendus au pied du haut fourneau par des cheminées latérales[T 6]. Puis, en 1850, apparait à Ebbw Vale le système de fermeture du gueulard avec une cloche, qui s'impose progressivement[T 7].
Les gaz de haut fourneau, qui ont traversé la charge, doivent être dépoussiérés pour ne pas colmater les fours : des pots à poussière, des cyclones et des filtres épurent ces fumées jusqu'à des teneurs en poussières de quelques milligrames par normo mètre cube[T 8]. Ces installations tiennent compte des contraintes liées à gestion d'un gaz toxique produit en de grandes quantités[L 6].
Cependant, les premières chaudières métalliques ne permettent guère de dépasser 400 °C. Si un appareil de briques réfractaires permet des fonctionnements à des températures plus élevées, la faible conductivité thermique du matériau amène à un fonctionnement fondé sur l'accumulation et la restitution de chaleur au lieu de la conduction[L 7].
Fort de ce constat, Edward-Alfred Cowper, un ingénieur britannique, dépose en 1857 un brevet intitulé Améliorations dans les fours pour chauffer l'air et autres fluides élastiques[SF 12]. Les premiers essais démarrent dès 1860, aux usines de Clarence[G 3], mais butent sur la tenue des briques, empilées en quinconce suivant l'idée de Carl Wilhelm Siemens, qui supportent mal le cyclage thermique[92],[L 8]. Il réagit en proposant la même année des améliorations qui préfigurent le four définitif : la flamme est éloignée des briques, qui comportent des canaux rectilignes[92].
Le Britannique Whitwell améliore sensiblement la tenue des réfractaires en faisant monter l'air entre des murs de briques plans. Cette disposition facilite aussi le nettoyage de l'ensemble[G 4], que la fumée due à la combustion encrasse rapidement. Il multiplie aussi les brûleurs et fonctionne en excès d'air pour éviter les points chauds[95].
Si les fours continueront encore d'évoluer, la mise au point des technologies permettant d'atteindre une température de 1 000 °C en utilisant une énergie jusque là inutilisée s'achève alors : les cowpers deviennent indissociables du haut fourneau.
1784, le puddlage
[modifier | modifier le code]Mise au point et perfectionnement
[modifier | modifier le code]
A : sole avec l'ouverture qui permet au puddleur d'y passer son ringard. Le crochet au-dessus permet l'ouverture de la trappe.
C : cheminée avec couvercle réglant le tirage pour réguler la chauffe.
D : Séparation entre le foyer et la sole pour éviter le contact entre fonte et combustible.
F : Foyer.
La pénurie de charbon de bois au XVIIIe siècle impose son remplacement par des combustibles minéraux. Or la production d'acier naturel, qui consiste à placer la gueuse de fonte au milieu du foyer, exposerait le métal aux cendres et aux fumées issues de la combustion du charbon[L 9] :
« Les feux d'affineries ne se prêtaient pas à cette substitution qui mettaient en contact le fer avec une matière toujours plus ou moins sulfureuse. Il fallait donc disposer de fours où le métal ne touchât pas le combustible solide et fût exclusivement soumis à l'action d'une flamme.[…]
C'est en poursuivant cette idée que l'anglais Cort imagine en 1784, le procédé d'affinage auquel on a donné le nom de puddlage du mot anglais to puddle qui signifie brasser. »
— A. Ledebur, Manuel théorique et pratique de la métallurgie du fer, p. 366
Invention complétant le haut fourneau au coke, le four à reverbère de Cort permet donc d'affranchir la filière sidérurgique du charbon de bois. Mais son avantage se limite au combustible : la combustion du carbone de la fonte, qui se fait par un courant d'air, est lente, ce qui entraîne une forte consommation de charbon ainsi qu'une oxydation importante du métal[L 10]. Consommant plus de deux tonnes de fonte blanche[note 14] pour produire une tonne de fer[T 9], le procédé de Cort permet l'obtention de fer en quantité mais sans réduire significativement les coûts.
En 1818, l'invention de la sole sur plaque de fonte refroidie à l'eau par Samuel Baldwin Rogers, complétée quelques années après par celle de Joseph Hall, qui adopte un garnissage réfractaire oxydant[T 10] permet de tripler la production d'un four. Ce garnissage, constitué d'oxydes de fer, réagit avec la fonte et accélère le processus. Il faut alors moins de combustible et les pertes par oxydation sont réduites[L 10] à près de 5 %[G 5].
Ces améliorations sont fondamentales[note 15]. Le procédé amélioré, appelé « puddlage gras », par opposition à la méthode primitive de Cort, le « puddlage sec »[note 16], se répand rapidement[G 5] :
« Dans les voyages métallurgiques de MM. Dufrénoy, Coste et Perdonnet, on voit (1re édition) qu'en 1823 l'usage des soles en sable était encore général. Vers 1820, on commence à substituer des scories pilées au sable. En 1829, on constate çà et là des soles en fonte, mais les auteurs ajoutent qu'en puddlant directement sur la fonte (sans couche de riblons ou de scories), les résultats étaient défectueux. Enfin, en 1837 (2e édition), les soles en fonte sont d'un usage général. »
— E.-L. Grüner, Traité de métallurgie, p. 168, note de bas de page
Le procédé
[modifier | modifier le code]Le puddlage commence par la préparation de la sole. Le puddleur dépose sur la sole la couche de scories et d'oxydes qui devient une croute sous l'action conjuguée de la chaleur du four et du refroidissement de la sole en fonte[L 11]. Les gueuses de fonte sont alors chargées sur cette couche d'oxydes. Le puddlage gras pouvant se faire sur sole basique, il est possible de traiter des fontes riches en silicium ou en phosphore[L 12].

Dès que la fonte commence à fondre, le puddleur intervient. Son travail se déroule dans des conditions difficiles et demande un évident savoir-faire :
« … le travail de l'ouvrier consiste […] à labourer la fonte et les scories à l'aide d'un fort ringard, recourbé à angle droit à son extrémité[…]. On mêle ainsi les particules métalliques aux éléments oxydés et les expose tous deux à l'influence de l'air. Pour opérer le brassage, on n'ouvre pas la porte de travail elle-même. L'ouvrier éprouverait une chaleur trop vive, et le four lui-même serait refroidi. On se contente d'introduire les outils par une simple ouverture de 0,10 à 0,15 m de côté, pratiquée dans le bas de la porte mobile, et facile à clore…
À mesure que le fer s'épure, il devient moins fusible[note 17] ; il faut donc, pour continuer le brassage, graduellement relever la température, en rouvrant peu à peu le clapet de la cheminée[G 6]. »
— E.-L. Grüner, Traité de métallurgie
La décarburation de la fonte provoque un bouillonnement, correspondant au dégagement de monoxyde de carbone. Lorsque celui-ci cesse, on peut encore pousser la décarburation jusqu'à obtenir du fer. Lorsque le puddleur l'estime finie, il partage la masse métallique en quelques boules. Celles-ci sont pressées dans le four pour les purger des scories[L 13].
L'extraction de ces boules hors du four est immédiatement suivie d'un martelage ou laminage pour en extraire un maximum de scories et donner une forme exploitable, généralement des barres. Pendant cette phase, le comportement du métal chaud permet de juger sa qualité[L 14].
Outre le brassage, la qualité du fer puddlé dépend aussi de la vitesse et de la rigueur avec laquelle il a été cinglé. Le métal obtenu consiste en effet en une matrice de fer contenant des scories de puddlage et des oxydes formés sur la surface des boules de fer brut pendant le cinglage[Ba 1]. Le forgeage des barres oriente ces impuretés de façon à limiter leur nocivité. Il faut pour cela des forgeages répétés et des outils puissants : c'est l'ère des marteaux-pilons, qui sont à la fois capables de parfaire le cinglage et de forger avec précision de grandes pièces[P 1].
L'acier au creuset
[modifier | modifier le code]Les fers obtenus par puddlage se prêtent bien à la cémentation. Mais la recarburation reste superficielle, le métal obtenu est hétérogène :
« Anciennement, l'acier n'était jamais fondu ni coulé après sa fabrication ; dans un seul cas, celui du wootz, il était fondu pendant la fabrication même. Quelle que fût la méthode […] l'acier en masse n'était pas obtenu à l'état homogène. Même par la cémentation du fer en barres, certains défauts qui se manifestent dans la fabrication du fer, surtout ceux inhérents à la présence des laitiers, se perpétuaient plus ou moins dans l'acier en barres[…]. Or la fusion et le moulage de l'acier remédient au mal signalé, et l'on peut ainsi se procurer des lingots d'une composition parfaitement homogène dans toutes leurs parties. C'est à Benjamin Huntsman que l'on est redevable de la solution pratique de cet important problème[P 2]. »
— J. Percy, Traité complet de métallurgie
Fabricant d'horloges, de serrures et d'outils divers, Benjamin Huntsman est insatisfait de la qualité des aciers qu'il travaille. Il mène des expériences pour produire un acier de meilleure qualité. Il développe son procédé, consistant à fondre des charges de 34 livres (soit 15,4 kg) dans des creusets en terre cuite. Le creuset, rempli de morceaux d'acier, est fermé, puis est chauffé avec du coke pendant près de 3 heures. L'acier en fusion est alors coulé dans des moules et les creusets sont réutilisés[P 3].
La qualité obtenue permet, par exemple, de réaliser des ressorts très performants pour l'horlogerie, tel que celui du chronomètre de marine de Harrison pour mesurer la longitude. La méthode est par contre mal adaptée à la production de pièces volumineuses, mais de nombreuses améliorations vont rapidement voir le jour pour traiter ce problème. Krupp s'y distingue, parvenant à couler un lingot de 2,25 tonnes en 1851, et de 21 tonnes en 1862[P 3].
Pourtant, l'industrie locale refuse d'utiliser cet acier, car il s'avère plus dur que celui qui était jusqu'ici importé d'Allemagne. À ses débuts, Hunstman n'a donc pas d'autre choix que d'exporter son métal en France. Mais la concurrence grandissante des couteaux français, réalisés à partir de l'acier au creuset inquiète les coutelleries de Sheffield. Après avoir, sans succès, tenté d'interdire l'exportation d'acier au creuset, les industriels anglais sont contraints d'adopter cet acier[97].
Huntsman n'a pas breveté son procédé et, se souciant guère de sa prospérité, « jamais il ne consentit à faire prospérer ses affaires par aucun des moyens si communs aujourd'hui[P 4] ». Son secret est éventé par un concurrent nommé Walker[note 18]. La diffusion du savoir-faire amène une expansion spectaculaire de la production d'acier à Sheffield. Alors qu'avant l'invention de Huntsman, en 1740, moins de 200 tonnes d'acier y étaient produites par cémentation, un siècle après, la production d'acier au creuset atteint 20 000 tonnes d'acier : de Sheffield sort 40 % de l'acier produit en Europe[99]. En 1860, la production d'acier de Sheffield dépasse 80 000 tonnes, soit plus de la moitié de la production mondiale.
Le monopole anglais d'acier cémenté fondu au creuset est brisé en 1805 par l'Allemand Johann Conrad Fischer (en)[100].
L'acier industriel
[modifier | modifier le code]1856, le procédé Bessemer
[modifier | modifier le code]La découverte
[modifier | modifier le code]
Henry Bessemer est un ingénieur et inventeur anglais fécond. Dans les débuts des années 1850, il cherche à fondre le fer et l'acier pour contourner l'opération de cinglage. Pour ne pas polluer le métal, il doit employer un four à réverbère, dans lequel il dose de la fonte et du fer pour obtenir de l'acier. Pour atteindre les températures nécessaires[note 19], il provoque un courant d'air à la surface du bain de métal liquide afin de parfaire la combustion des fumées[B 1].
Il observe alors que, à la surface de la fonte liquide, se forment de fines plaques de fer décarburé. Ce fer, solide car sa température de fusion est supérieure à celle de la fonte, a été obtenu par la seule action de l'air « sans puddlage ou autre manipulation[B 2] ». Il décide alors de réorienter ses recherches pour mieux comprendre cette découverte. Pour cela, il construit un creuset de laboratoire avec une canne permettant d'injecter de l'air dans de la fonte en fusion. Cet outil expérimental lui permet d'obtenir du fer liquide[B 3].
Ce creuset est réchauffé par l'extérieur. Or Bessemer, qui connait la nature exothermique des réactions d'affinage, veut savoir si la chaleur apportée par la réaction est suffisante pour non seulement compenser la perte thermique due à l'apport d'air froid, mais aussi élever la température jusqu'à celle de fusion du fer[note 4],[B 3].
La méthode imaginée par Bessemer soulève beaucoup de scepticisme[B 4]. Ainsi, il raconte cet échange avec son contremaître qui résume l'opinion générale :
« « Où voulez-vous mettre le métal, monsieur ? »
Je lui répondis : « Je veux que vous le versiez à l'aide d'une rigole dans ce petit four », en lui désignant le convertisseur, « celui dont vous avez arrêté tout le chauffage et dans lequel je dois souffler de l'air froid pour le réchauffer ». L'homme me regarda d'un air où la surprise et la pitié pour mon ignorance étaient curieusement mêlées.
Il dit alors : « il sera vite pris en masse »[B 5]. »
— Henry Bessemer, Sir Henry Bessemer, F.R.S, an autobiography
Le premier essai est pourtant couronné de succès. Encouragé par George Rennie, président de la section mécanique de la British Association, il se rend le 13 août 1856 à Cheltenham pour expliquer son procédé devant le congrès de cette association renommée. Son discours a un grand retentissement et est reproduit le lendemain dans The Times[B 6].
Le convertisseur Bessemer
[modifier | modifier le code]
Bessemer essaie diverses formes de fours. Ceux-ci s'avèrent peu adaptés au process : il faut pouvoir stopper rapidement et à tout moment l'affinage sans endommager les tuyères, les formes internes doivent être concaves pour améliorer la tenue du réfractaire, les installations d'amenée de la fonte liquide doivent être éloignées du bec pendant le soufflage[B 7]… Il résout le problème en créant un convertisseur rotatif en forme de cornue :
« J'ai activement cherché une solution pour ces graves défauts sans succès, jusqu'au moment où j'ai eu l'idée de monter le convertisseur sur des axes ; ainsi je pouvais maintenir les tuyères au-dessus du métal jusqu'au moment où la totalité de la fonte en fusion était dans le convertisseur. Cela permet la réalisation du soufflage de la totalité de la charge en même temps et permet également l'arrêt de la soufflerie pendant le déchargement. Ce mouvement du convertisseur permet un arrêt de l'opération à tout moment pour réparer une tuyère endommagée et facilite énormément le travail[B 7]. »
— Henry Bessemer, Sir Henry Bessemer, F.R.S, an autobiography
En même temps que le convertisseur, Bessemer met au point tous les outils annexes. Une usine de démonstration est alors édifiée à Sheffield ; après deux ans de fonctionnement, elle devient rentable[B 8]. Aux maîtres de forges qui achètent le droit d'utiliser le nouveau procédé en échange d'une redevance de dix shillings par tonne de métal produite, Bessemer propose les plans d'un outil parfaitement au point. Thomas Turner constate, une cinquantaine d'années après l'annonce de Cheltenham, qu'il est « remarquable que non seulement la première conception, mais aussi les détails mécaniques du procédé sont tous issus du même esprit, et que l'invention a quitté les mains de son concepteur si aboutie qu'aucune amélioration, excepté des détails mineurs, n'a été depuis introduite[T 11] »[note 20].
L'élaboration de l'acier Bessemer
[modifier | modifier le code]
Pendant les premiers essais, la violence de la réaction est telle que, pour Bessemer, le procédé lui semble « condamné en tant qu'outil commercial, à cause des projections de laitier, et uniquement pour cette raison[B 9] ». Les améliorations qu'il apporte au four lui permettent finalement de gérer les projections. Celles-ci s'avèrent même essentielles pour évaluer l'avancement de l'affinage[L 15] :
- la combustion du silicium, qui est le principal contributeur thermique (la combustion de 1 % de silicium élève la température du bain de 300 °C[L 16]) intervient en premier. Cette phase se manifeste par des projections d'étincelles jaunes et une courte flamme orange ;
- la combustion du carbone est identifiable par l'apparition d'une longue flamme d'un blanc éclatant. La combustion générant de grandes quantités de monoxyde de carbone, le bain de métal liquide est violemment agité. Par contre la faible contribution thermique du carbone est rapidement admise par tous[L 16], alors que Bessemer l'avait estimée fondamentale[B 10] ;
- la combustion du fer intervient à la fin de la réaction. Elle génère des fumées rousses, caractéristiques de l'oxyde de fer. Sans intérêt thermique[L 16], cette phase correspond à un gaspillage de fer affiné.
Pour l'opérateur, il est donc facile de distinguer les différentes phases du soufflage. Pourtant, les quelques maîtres de forge qui ont acheté le droit d'utiliser le procédé de Bessemer s'avèrent incapables d'obtenir un métal utilisable : celui-ci est cassant à froid et se désagrège s'il est travaillé à chaud. Recherchant soigneusement l'origine de la mauvaise qualité du fer obtenu avec certaines fontes, il constate que « la fonte brute britannique contient de façon abondante cet ennemi mortel, le phosphore[B 11] ».
En effet, le fer, lorsqu’il contient plus de 3 ‰ de phosphore, devient cassant[Ba 2]. Pour Bessemer, qui avait initialement dirigé ses recherches vers l'obtention d'un acier de haute qualité pour la fabrication de canons[B 12], c'est un coup dur. Les premiers essais de son procédé, réalisés avec une fonte suédoise au charbon de bois, avaient donné un fer doux de qualité satisfaisante. La recherche d’une amélioration capable d’ôter le phosphore mobilise l’énergie de Bessemer pendant plusieurs années. Mais, après la dépense de plusieurs milliers de livres sterling en expérimentations diverses[B 13], il ne trouve pas de solution pour l'éliminer[101]. Même en rachetant les droits de ses associés, Bessemer ne parvient pas à étouffer l'affaire, qui s'ébruite jusque dans la presse[B 14] :
« Je me suis permis d'apporter trop rapidement mon invention devant l'intérêt du public. Je n'aurais pas dû le faire avant que tous les détails du procédé n'aient été examinés, et j'en aurais alors fait un grand succès commercial (et non pas scientifique)[B 15]. »
— H. Bessemer, Sir Henry Bessemer, F.R.S; An autobiography, p. 164
Si le puddlage s’avère capable de retirer le phosphore d’une fonte moyennement phosphoreuse[P 5],[P 6], les réactions qui permettent ce résultat sont encore mal comprises[L 17],[Ba 3]. On ne sait pas encore que « la combustion du phosphore se fait en formant de l'acide phosphorique (P2O5) qui ne peut subsister que s'il est fixé par une scorie basique[C 1] ». Mais une scorie basique n'agit que si aucun autre matériau acide ne vient prendre la place de l'acide phosphorique. Or Bessemer, dont le procédé fonctionne avec du fer liquide, et non pas pâteux, doit utiliser un revêtement réfractaire plus performant que ceux convenant au puddlage. Mais à cette époque, seuls les réfractaires à base de silice, donc très acides, sont capables de résister aux sévères conditions régnant dans le convertisseur[L 18].
L'acier Bessemer supplante le fer puddlé
[modifier | modifier le code]
Mais Bessemer propose, plus qu'un procédé et l'usine associée, un nouveau matériau : l'acier liquide. En effet, la présence d'une grande quantité d'oxygène dissous dans le fer liquide à la fin du soufflage impose un traitement complémentaire. Une addition de spiegeleisen, une fonte de manganèse qui se combine avec l'oxygène pour former un oxyde de manganèse, s'avère idéale[101],[B 16]. Mais ce ferroalliage recarbure aussi le fer. Cette recarburation est finalement une opportunité, car elle transforme le fer en acier[T 11]. Le procédé, mal adapté « à la production de fer doux, devient, avec quelques modifications, capable de produire de l'acier de bonne qualité, avec une grande étendue de composition et de solidité[Ba 4] ».

Bessemer ne perd pas de vue que ses premiers essais consistaient à réaliser un métal coulé dont la qualité, contrairement au fer puddlé, ne dépend pas du cinglage puisqu'il est exempt de laitier. En dépit de la mauvaise réputation initiale de l'acier Bessemer, autant due à l'annonce prématurée faite à Cheltenham[B 15], qu'à l'ignorance des maîtres de forges qui ignorent tout de la sensibilité de l'acier aux traitements thermiques[B 17], il insiste sur la supériorité du métal affiné au vent.
Ses efforts ne sont pas isolés : la métallurgie scientifique succède aux méthodes empiriques qui ont donné naissance aux procédés précédents. L'acier Bessemer, qui se généralise dans la production de rails[B 17], progresse pour devenir compatible avec les applications les plus exigeantes, comme les canons et les chaudières[B 18].
L'industrialisation de ce métal est en route. Dès le début des années 1860, les métallurgistes français Gruner et Lan affirment sans détour qu'« il est bien évident pour nous que l'acier puddlé, ainsi que le fer puddlé aciéreux (fer à grains), ont fait leur temps. Ils vont céder le pas à l'acier Bessemer, comme ils ont remplacé eux-mêmes l'ancien acier de forge et l'acier cémenté plus ou moins corroyé[102]. »
1877, Thomas et Gilchrist déphosphorent la fonte
[modifier | modifier le code]Comment convertir les fontes phosphoreuses ?
[modifier | modifier le code]Inacapable de déphosphorer la fonte, Bessemer se résout à limiter son procédé à l'affinage de fontes suédoises au charbon de bois et de quelques fontes hématites anglaises, élaborées à partir de minerais sans phosphore. Le procédé reste rentable car son efficacité compense le coût plus élevé des fontes de qualité[B 19]. Il n'est guère prisé qu'aux États-Unis, en Grande-Bretagne et, dans une moindre mesure, en Suède, les seuls pays dont la production sidérurgique décolle[103].
Or de nombreux pays ne possèdent que des minerais de fer phosphoreux. C'est le cas de la France avec la minette lorraine, mais aussi de l'Allemagne, de la Belgique, du Luxembourg et même du Pays de Galles. Non seulement de nombreux industriels ne peuvent utiliser le procédé, mais à cause de la forte demande, les minerais non phosphoreux deviennent extrêmement coûteux. De nombreux chercheurs se penchent sur le problème de la déphosphoration. Les réactions chimiques sont progressivement découvertes.
L'oxydation du phosphore donne un acide dont la forme anhydre à haute température est le pentoxyde de phosphore P2O5, qui se forme au cours de la réaction suivante[104] : 2 P + 5 O P2O5
Toutefois, comme le montre le diagramme d'Ellingham, cet oxyde de phosphore est décomposé par le fer suivant la réaction : P2O5 + 5 Fe → 2 P + 5 FeO dès que T > 1 280 °C[104].
Si la déphosphoration au puddlage, qui opère sur du fer à relativement basse température, n'est que peu pénalisée par cette réaction, il n'en est pas de même dans un convertisseur. En effet, la température y est beaucoup plus élevée car, en fin de soufflage, elle correspond au moins à celle du fer en fusion (1 535 °C). Pour s'affranchir de cette réaction, il faut qu'un oxyde basique se combine avec l'oxyde acide P2O5 dans le laitier dès sa création. On parvient ainsi à la fois à stabiliser le phosphore sous une forme oxydée, et à diminuer l'activité du P2O5 de façon à favoriser sa création[104].
Dans le début des années 1870, les premiers résultats commencent à être publiés. Un certain Heaton réussit à déphosphorer de la fonte liquide en employant du nitrate de sodium, Snelus brevette l'utilisation de chaux[Ba 5],[T 12],[Cr 1], Bell met au point un procédé utilisant la magnésie et l'oxyde de fer[105]… En effet, l'oxydation du phosphore en présence d'un excès de chaux permet en effet la création d'un phosphate stable, selon la réaction :
2 P + 5 FeO + n CaO → n CaO.P2O5 + 5 Fe avec n = 3 ou 4[106],[104].
Cependant, l'idée bute sur l'impossibilité d'élaborer un revêtement réfractaire stable. Le revêtement réfractaire adopté par Bessemer est siliceux, donc très acide. Toute base présente dans le four se combinerait avec la silice préférentiellement à l'oxyde de phosphore, beaucoup moins acide : il faut donc mettre au point un réfractaire basique. Or il n'existe pas de revêtement basique industriellement utilisable :
« Le carbonate de chaux est décomposé par la chaleur ; la chaux vive absorbe l'humidité et tombe en poudre… Le jour où l'on met hors feux, la chaux fuse et tombe en poudre. La magnésie conviendrait mieux, parce qu'elle ne se délite pas à l'air ; malheureusement le carbonate de magnésie est une rareté minéralogique. Peut-être pourrait-on avoir recours à la dolomie, le carbonate double de chaux et de magnésie ? La dolomie, cuite à haute température, surtout si elle contenait assez d'argile pour se fritter un peu, résisterait mieux que la chaux pure à l'action de l'air humide[G 7]. »
— E.-L. Grüner, Traité de métallurgie
L'invention de Thomas
[modifier | modifier le code]
L'intuition de Grüner est la bonne. Mais ce sont deux Anglais qui vont faire la découverte et mettre au point la méthode.
Sidney Gilchrist Thomas a 25 ans quand il pense trouver la solution. Il sollicite l'aide de son cousin Percy Carlyle Gilchrist, chimiste à la Blaenavon Ironworks, dans le pays de Galles. Ils s'attellent à la mise au point d'un revêtement réfractaire basique en testant divers additifs pour stabiliser la chaux. Dans sa version finale, le réfractaire consiste en de la dolomie broyée puis cuite et mélangée avec du goudron[107],[Cr 2]. La cuisson de la dolomie est une calcination qui rend le minéral apte à supporter les hautes températures tandis que le goudron sert à la fois de liant et d'imperméabilisant[L 19].
Les essais de laboratoires commencent en 1877 à la Blaenavon Ironworks. Sidney Thomas dépose alors un brevet pour protéger son invention. Des essais à l'échelle industrielle sont ensuite réalisés à Dowlais Iron and Co[Cr 2]. Les succès constatés dans cette usine décident les deux cousins à publier leur invention. Comme Bessemer à Chelteham, ceux-ci préparent une intervention pour le congrès de l'Iron and Steel Institute de l'automne 1878, qui se déroule à Paris. Mais leur exposé est jugé sans intérêt et sa lecture est repoussée à la session suivante. Pourtant, le problème de la déphosphoration intéresse au plus haut point la communauté des sidérurgistes. Le renommé métallurgiste Bell, qui inaugure ce congrès en présentant ses recherches sur la déphosphoration, amène un débat dans lequel Thomas intervient discrètement[Cr 3] :
« Au milieu de cette discussion, un jeune membre, apparemment le plus jeune de l'assemblée, rapporta modestement en trois phrases qu'il venait de réussir à ôter la quasi-totalité du phosphore dans le procédé Bessemer, et que plusieurs centaines d'analyses réalisées par M. Gilchrist confirmaient une diminution de 20 à 99,9 % du phosphore. Personne ne rit, ni ne félicita ce jeune homme pour cette réussite. On ne se renseigna pas plus sur sa méthode d'élimination ; cette annonce peu démonstrative ne fut même pas remarquée. Ce jeune homme, dont le nom n'était connu que de peu de gens présents là, était Sidney Gilchrist Thomas, et le procédé Thomas-Gilchrist venait d'être annoncé pour la première fois[Cr 4]. »
— William Tulloch Jeans, The Creators of the Age of Steel
Pendant l'hiver, Thomas apporte les derniers perfectionnements à son procédé. Le 4 avril 1879 une production industrielle démarre dans l'usine de Bolckow Vaughan de Middlesbrough[108], sur un convertisseur d'une capacité de 15 tonnes. Les directeurs des usines où se sont déroulés les essais assurent la publicité du nouveau procédé. La rumeur se répand alors et « Middlesbrough est rapidement assiégée par les forces combinées de Belgique, France, Prusse, Autriche et d'Amérique[Cr 5] ». Le congrès de l'Iron and Steel Institute du printemps 1879 consacre le succès des deux cousins et des maîtres de forges qui s'étaient associés à eux. Dès le mois d'août, des aciéries d'Europe continentale[note 21] font part de leurs succès[Cr 7].
Le procédé
[modifier | modifier le code]À part le revêtement, le procédé est très proche du procédé « acide » Bessemer. L'oxydation du phosphore impose quelques opérations complémentaires : on verse préalablement dans la cornue une charge de chaux vive correspondant à 12 à 15 % du poids de la fonte, puis on enfourne la fonte. Enfin le soufflage est prolongé au-delà de la décarburation pour permettre la déphosphoration[L 20].

Les opérations de désilication et de décarburation sont semblables à celles du procédé acide ; seule la cinétique des réactions change, la basicité du laitier favorisant la production de silice mais gênant celle d'oxyde de manganèse[Ba 6].
Pendant la déphosphoration, le phosphore oxydé migre dans le laitier. La forte élévation de la température s'explique par l'aspect très exothermique de l'oxydation de cet élément. Cette dernière étape, appelée « sursoufflage », doit être arrêtée dès que le phosphore est éliminé car elle correspond aussi au début de la combustion du fer, qui se manifeste par l'émission de fumées rousses[Ba 7].
Le phosphore ne s'éliminant qu'à la fin du soufflage, la combustion complète du carbone est un préalable à l'élimination du phosphore. Si l'on veut augmenter le taux de carbone de l'acier, il faut recarburer ensuite de manière contrôlée le métal en fusion. Cette recarburation doit se dérouler après la vidange du laitier pour éviter que le phosphore ne retourne dans le métal[L 21].
L'acier obtenu est séparé, par décantation, du laitier contenant les oxydes de phosphore. Cette scorie est utilisée comme engrais. Sidney Thomas, qui s'implique également dans l'amélioration des conditions sociales de son temps, promeut cette qualité. L'acide phosphorique qui s'y trouve se présente sous forme de phosphate tétracalcique (P2O5, 4 CaO) dont la majeure partie est assimilable par la végétation. La quantité de scories est d'environ 200 à 250 kg de scorie par tonne d'acier[C 2].
Les conséquences sur l'économie
[modifier | modifier le code]Le nouveau procédé permet l'utilisation intensive des minerais phosphoreux et en particulier l'utilisation du minerai lorrain. Ce minerai, riche en phosphore (d'environ 0,5 à 1 % du minerai), restait inutilisable avec un revêtement acide, la déphosphoration nécessitant un laitier riche en chaux, donc basique.

Dans quatre pays les plus industrialisés (Allemagne, États-Unis, France et Grande-Bretagne), la proportion d'acier Thomas, proche de zéro en 1880, correspond à 62 % de la production Bessemer et Thomas en 1913[109], sachant que la production américaine connait une croissance spectaculaire (3 380 kt en 1880 et 33 500 kt en 1913) sans utiliser le procédé Thomas[103].
En 1880, le Royaume-Uni produit 1,31 Mt d'acier liquide alors que quatre autres pays européens, Allemagne, Belgique, France et Luxembourg, n'en produisent que 1,22 Mt[109]. À la veille de la Première Guerre mondiale, en 1913, ce pays a perdu sa position dominante. La production allemande d'acier, qui profite des gisements de la Lorraine annexée[note 22] et de la cartellisation des industriels, représente, en 1908, 11,2 Mt contre 5,3 Mt pour le Royaume-Uni, la production au four Martin atteignant alors dans chacun des deux pays environ 4 Mt[103].
Le nouveau procédé a donc complètement modifié le poids industriel des nations, notamment en Europe. Compte tenu également du niveau des investissements, c'est aussi le démarrage du règne des grandes entreprises qui sont capables d'intégration verticale et/ou de spécialisation.
À l'intérieur des pays, la production métallurgique se concentre dans certaines régions. En France, de nombreux petits centres métallurgiques ruraux qui avaient survécu à l'arrivée et aux perfectionnements des hauts fourneaux au début du XIXe siècle[G 8] disparaissent au profit notamment de la Lorraine non annexée. En 1869, avant la guerre franco-allemande de 1870, les deux départements de Meurthe et de Moselle produisent 1,4 % de l'acier français ; en 1913 l'acier Thomas des usines de la seule Meurthe-et-Moselle correspond à 69 % de la production nationale[F 9]. Cette évolution est aussi accentuée par la très forte amélioration des moyens de transports qui permettent la livraison des produits manufacturés loin des centres de production.
1864 : Pierre-Émile Martin fait fondre l'acier
[modifier | modifier le code]Principe de fonctionnement du four Siemens :
|
Les fours à réverbère de la première moitié du XIXe siècle ne fournissent pas une température suffisante pour faire fondre l'acier. En 1864, le Français Pierre-Émile Martin réussit à Sireuil, dans l'usine de son père Émile Martin, à mettre au point un four à réverbère permettant de faire fondre un mélange de fonte et de riblons (déchets de production de fer ou d'acier inutilisable en l'état) ou de ferrailles recyclées. L'utilisation du procédé Martin présente un grand intérêt économique grâce à l'utilisation des déchets de fer et d'acier qui, du fait du développement de la production, commencent à représenter des quantités importantes. La durée de l'opération d'affinage prend un temps plus long en comparaison avec le procédé au convertisseur. Ce point, s'il est un désavantage pour la productivité, présente le grand avantage de permettre une meilleure maîtrise du procédé et ainsi d'obtenir des aciers de meilleure qualité. Rapidement, les « aciers Martin » sont choisis pour l'armement (le fusil Chassepot, les canons de la marine française) ou les bandages des roues de chemin de fer.
Le four Siemens-Martin
[modifier | modifier le code]Pierre-Emile Martin réussit à mettre au point son procédé de fabrication en utilisant selon ses recherches une technologie de four mise au point en 1856 par Carl Wilhelm Siemens dont il a acquis la licence. La technologie de ces fours repose sur le préchauffage des gaz de combustion dans quatre chambres remplies de briques réfractaires empilées en chicane ou en domino pour présenter une grande surface de contact.
L'installation est constituée d'un four à sole et de quatre régénérateurs de chaleur. Ces derniers sont des chambres revêtues de matériau réfractaire dans lesquelles on empile des briques. Ces briques servent d'accumulateurs de chaleur. Les gaz de combustion sont récupérés à une température supérieure à 1 500 °C à la sortie de four et sont dirigés vers deux des chambres. Les briques récupèrent la chaleur de ces gaz. Lorsqu'elles atteignent une température suffisante, le flux gazeux est inversé à l'aide d'une vanne. Le gaz carburant ainsi que l'air comburant sont alors dirigés vers ces deux chambres afin de s'échauffer avant d'être dirigés vers le four. Ils arrivent au niveau du brûleur (appelé le carmeau) dans le four à une température importante, ce qui a pour effet d'augmenter significativement la température à l'intérieur du four.
L'utilisation de ce type de four est limitée à cause de la fragilité des réfractaires utilisées pour la fabrication de la sole. Il n'est utilisé que pour le puddlage ou dans les verreries. Pierre-Emile Martin réussit à mettre au point une sole réfractaire siliceuse (donc acide) qui résiste à la température :

« Dans la plupart des fours, ce pisé se compose de quartz aussi pur que possible broyé sous forme de sable à gros grain de la grosseur d'un pois que l'on mélange avec une quantité d'argile réfractaire qui varie de 2 à 5 %, et qui assure l'agglomération. Tantôt on établit la sole en une seule fois sur toute son épaisseur, puis on laisse sécher lentement, après quoi on procède à la cuisson en élevant graduellement la température, tantôt on la construit par couches successives de 20 millimètres que l'on cuit l'une après l'autre[L 22]. »
— A. Ledebur, Manuel théorique et pratique de la métallurgie du fer
En 1879, les ingénieurs français Varlands et Alexandre Pourcel à Terrenoire (près de Saint-Étienne) et au Creusot, utilisant les travaux de Thomas, mettent au point des soles basiques fabriquées à partir de magnésie et de dolomie. Ce type de sole permet, exactement de la même manière que pour les convertisseurs Thomas, de traiter des matières premières qui contiennent du phosphore.
Les traducteurs de l'ouvrage de Ledebur mentionnent également l'existence de sole dite « neutre » contenant du ferrochrome. Contrairement aux deux autres types de soles, elle ne joue aucun rôle dans les réactions métallurgiques avec le métal en fusion[L 23].
Les matières premières
[modifier | modifier le code]Le grand intérêt du procédé Martin est la possibilité de recycler du fer ou de l'acier sous forme de riblons ou sur forme de ferraille récupérée :
« La principale matière première formant la charge d'un four Martin est le fer doux sous forme de débris, de riblons de toutes sortes, de bout de barres laminés, de ferrailles, etc. ; en somme, il n'existe guère de morceau de fer de quelques qualités qui soit, dont on ne puisse tirer parti au four Martin[L 24]. »
— A. Ledebur, Manuel théorique et pratique de la métallurgie du fer
L'autre grande matière première est la fonte. Pendant la transformation, la fonte est affinée en perdant son carbone et son silicium. Plus la proportion de fonte est importante (ce qui augmente la proportion de carbone dans le mélange), plus l'affinage doit être énergique.
La proportion entre la quantité de déchets ferreux et la fonte est extrêmement variable, allant à l'extrême jusqu'à des charges ne contenant que de la fonte. D'après Colombier, la quantité minimum de fonte est de 20 % pour le procédé acide[C 3].
Dans les fours à sole basique, on peut utiliser directement du minerai de fer pour le procédé dit « au minerai ». Afin de déphosphorer la charge dans ce type de four, on utilise également de la chaux ou du calcaire.
« … il se présente certaines circonstances où l'on est amené à préférer un dosage de matières comportant plus de fonte et moins de fer […] Souvent, c'est en se basant sur le prix relatif de la fonte et des ferrailles que l'on établit la composition du lit de fusion, et rien ne s'oppose à ce que la proportion de fonte soit plus élevée, si on augmente les réactions oxydantes pendant la fusion. Le moyen le plus simple qu'on puisse employer pour atteindre ce but, consiste dans l'addition de minerai de fer, dont l'oxygène intervient pour brûler le carbone ; une partie du fer de ce minerai est réduit et vient s'ajouter à celui du bain[L 25]. »
— A. Ledebur, Manuel théorique et pratique de la métallurgie du fer
Le procédé
[modifier | modifier le code]Le four est chargé manuellement ou mécaniquement. L'ordre et la disposition de chargement dépendent de nombreux facteurs. Ledebur note par exemple en 1895 que dans les petits fours, le fondeur charge d'abord la fonte en une seule opération ; il attend qu'elle soit fondue avant d'ajouter par opérations successives le fer et l'acier. Alors que dans les grands fours, et notamment ceux à sole basique, on charge en même temps la fonte et les autres matières métalliques[L 26]. Colombier indique en 1957 que, pour le four à sole acide, on met la charge en une seule opération, d'abord la fonte sur la sole puis les riblons au-dessus de la charge[C 4].

Au XIXe siècle, la conduite de l'opération repose principalement sur le savoir-faire et le coup d'œil du fondeur qui conduit le four :
« L'oxydation du carbone se manifeste par le bouillonnement que produisent les bulles d'oxyde de carbone qui se dégagent du métal en fusion […] Quand le bouillonnement a cessé, ou s'est apaisé, on fait la première prise d'essai ; à cet effet, on plonge dans le bain une petite poche de fer préalablement chauffée, et on en retire un peu de métal qu'on verse dans un moule en fonte ; on obtient une éprouvette ; les étincelles qui se dégagent du métal pendant qu'on le coule, le boursouflement qui se produit dans le moule, ou le retassement sont déjà des indices de la nature du métal, on la porte sous le marteau, on la forge rapidement et on essaie de la plier à froid […] pour un œil exercé, le simple examen de la cassure suffit à montrer la décarburation du métal[L 26]. »
— A. Ledebur, Manuel théorique et pratique de la métallurgie du fer
Il faudra attendre de nombreuses années pour voir apparaître des appareils de mesure, notamment de la température. Colombier note dans son ouvrage : « on ne saurait trop insister sur l'importance qu'il y a à introduire le plus de mesures possibles dans l'élaboration de l'acier dont la conduite fut laissé si longtemps au flair acquis par une longue expérience »[C 5].
Lorsque l'opérateur juge que la décarburation est suffisante, divers éléments (ferromanganèse, ferrosilicium ou aluminium) sont ajoutés pour désoxyder et dégazer (« calmer ») la charge ; « Veut-on obtenir du fer doux destiné au laminage, l'addition se composera de ferromanganèse contenant de 50 à 80 % de manganèse, et son poids sera de 0,5 à 1 % du métal chargé. Pour obtenir du fer moins doux ou de l'acier, on ajoutera 1 à 3 % de ce ferromanganèse »[L 27].
Une fois l'ensemble des opérations réalisées, le métal obtenu est coulé dans une poche ou une lingotière.
L'affinage n'est pas réalisé par le passage de l'air à travers la charge de fonte, comme dans les convertisseurs, mais par le contact entre le métal en fusion et le laitier. La durée totale de l'opération est donc beaucoup plus longue et varie fortement en fonction de la proportion de fonte, de la nature de la sole, de la température du four et du temps employé au chargement (à cause du temps de chargement mais également du refroidissement du four si les portes restent ouvertes plus longtemps) et du poids de la charge. Ledebur donne un temps variant de 4 à 12 heures avec plus classiquement un temps variant de 5 à 8 heures. Ce qui permettait de faire trois à quatre coulées dans la journée[L 28]. La durée est un désavantage en termes de productivité mais est un avantage en termes de maîtrise de la qualité du produit obtenu. Le temps plus long et les possibilités d'ajustement ou d'addition dans la charge permettent d'obtenir des aciers de meilleure qualité en comparaison de ceux obtenus avec les procédés Bessemer et Thomas. Le procédé est aussi apprécié en termes de coûts par des fournisseurs d'armes ou de rails du centre de la France (Forges Verdié, Forges Terrenoire)[110], parfois en complément du Bessemer.
L'aciérie moderne
[modifier | modifier le code]Le retour limité à la réduction directe
[modifier | modifier le code]Alors que la suprématie du haut fourneau s'affirme dès le Ier siècle en Chine et au XIIIe siècle en Europe[SF 13], des bas fourneaux élaborés, comme le tatara ou la forge catalane, survivent jusqu'au XIXe siècle[G 9], grâce à leur taille contenue et à leur capacité à utiliser des minerais ou des combustibles mal adaptés au haut fourneau.
Ces procédés, dits de réduction directe, car ils produisent du fer en une seule étape au lieu de deux pour le couple haut fourneau - convertisseur, sont reconsidérés après l'invention de procédés économiques de fusion, comme le four Martin-Siemens ou le four électrique. En effet, le diagramme d'Ellingham montre qu'il suffit de se placer au-delà de 830 °C pour que le monoxyde de carbone réduise complètement le minerai de fer[111]. À partir de ce constat, des procédés très différents des bas fourneaux sont inventés dès la fin du XIXe siècle. Ils permettent la fabrication industrielle d'un minerai de fer préréduit bien plus homogène qu'une loupe. Des usines en exploitent quelques-uns avant la Seconde Guerre mondiale (procédé Chenot dans les années 1850[G 9], réduction directe de Siemens vers 1880[112], procédé Krupp-Renn dans les années 1930[113], etc.). Ils restent cependant confidentiels, leur rentabilité étant généralement discutée[L 29] :
« On a peine à comprendre aujourd'hui qu'on ait pu considérer à l'origine le procédé Chenot comme destiné à révolutionner l'industrie du fer, alors qu'il ne peut s'appliquer qu'à des minerais absolument purs, toutes les fois qu'on ne se résout pas à refondre l'éponge au creuset ou au four Martin. On ne comprend pas davantage que, dans une seule usine, dix fours aient pu être montés, représentant une dépense considérable, pour fabriquer un produit entraînant, par tonne d'éponge, une consommation de 1 400 kilos de charbon de bois pour la réduction et 1 723 kilos de houille pour le chauffage des cornues[114] : on ne pouvait transformer l'éponge en fer qu'en l'agglomérant au feu comtois au prix d'une nouvelle consommation de charbon et d'un déchet considérable[L 32]. »
— A. Ledebur, Manuel théorique et pratique de la métallurgie du fer
Une nouvelle génération de procédés de réduction directe apparait dans les années 1950. Les procédés étudiés[116] substituent le gaz naturel au charbon, en tant que combustible et agent réducteur. On constate alors que combiner le monoxyde de carbone avec de l'hydrogène à des températures d'environ 1 050 °C améliore à la fois la rapidité et la consommation thermique du processus de réduction[117],[118].
Le 5 décembre 1957, l'entreprise mexicaine Hylsa démarre à Monterrey la première usine de réduction directe au gaz naturel, le préréduit obtenu étant destiné à la fusion au four à arc électrique[119],[120]. La production de minerai préréduit avec du gaz naturel s'avérant économiquement viable, plusieurs usines sont construites à la fin des années 1960. Un approvisionnement en gaz naturel[123] bon marché étant essentiel à leur rentabilité, la plupart des usines se situent dans des pays disposant de gisements de gaz, en Amérique latine (où beaucoup ont été mis au point) et au Moyen-Orient[121].

Mis au point dans les années 1970, le procédé Midrex est le meilleur exemple de ces procédés réduction directe au gaz naturel. Succès technique autant que commercial, il représente depuis 1980 environ deux tiers de la production mondiale de préréduits. Fonctionnant en continu, il s'apparente à un haut fourneau dépourvu de creuset, accolé à une unité de production de gaz réducteurs chauds. Son concurrent direct, le procédé HYL III, concrétise un effort de recherche du groupe Tenova, héritier des pionniers mexicains de Hylsa. Assurant près de 20 % de la production de préréduits[122], il se distingue du Midrex par son unité de production des gaz réducteurs avec son reformage interne[124]. Ces deux procédés au gaz, techniquement matures et vendus clé en main, assurent une bonne visibilité financière aux investisseurs… en comparaison des espoirs souvent déçus des procédés concurrents[125].
Quant aux procédés au charbon, ils évoluent du tambour de réduction directe de Siemens[126], fondé sur l'utilisation d'un court tambour[112], vers un long four rotatif inspiré de ceux utilisés en cimenterie. Il s'agit là de brasser à haute température de la poudre de minerai de fer et du charbon, avec un peu de calcaire pour diminuer l'acidité du minerai. Le procédé Krupp-Renn démontre la viabilité du principe : développé dans les années 1930, il y a jusqu'à 38 fours en 1945 qui, quoiqu'ils ne totalisent alors qu'une capacité de 1 Mt/an[note 23], ont été installés partout dans le monde[113]. Si le succès du Midrex éclipse les évolutions ultérieures des procédés au charbon, quelques unités mises en service pendant la deuxième moitié du XXe siècle démontrent la rentabilité des variantes modernes des fours rotatifs de réduction[127].
À chaque fois qu'une innovation technique, ou que la conjoncture économique, déséquilibre les filières de production classiques, la réduction directe est réévaluée. De nombreux développements ont permis la mise au point de procédés au plasma[128], à l'oxygène, sur lit fluidisé ou sole tournante[129], etc. Il s'agit alors d'explorer des solutions innovantes pour fournir un substitut aux ferrailles (qui se raréfient dès les années 1960 avec le développement des aciéries électriques[113]), limiter les émissions de gaz à effet de serre[130], exploiter un gisement de gaz naturel, etc.
Pour autant, malgré le fait que la quantité d'acier produite à partir de préréduits croît de manière continue, et plus vite que la production mondiale d'acier, aucun procédé n'a été en mesure de supplanter la production au haut fourneau ou au four électrique. Après 40 ans de développements, la production d'acier issue de préréduits n'a jamais dépassé 5 % de la production mondiale d'acier[122],[SF 13]. Essentiellement fondée sur des procédés au gaz, elle reste cantonnée dans les pays producteurs de pétrole. En effet, en 1998, les sidérurgistes européens constatent encore que « pour être concurrentielle, la réduction directe doit disposer d'un gaz naturel à 2 dollars le gigajoule, la moitié des prix européens[131] ». Cependant, depuis 2005, les procédés au charbon reprennent de l'importance, portés par de nombreuses unités de production mises au point en Inde[129].
L'aciérie à l'oxygène
[modifier | modifier le code]En 1895, Carl von Linde réussit la liquéfaction de l'air. Indépendamment de cette démarche, Georges Claude met en service le un procédé industriel de liquéfaction de l'air. Leurs brevets autorisent la production industrielle, et surtout économique, de grandes quantités d'oxygène et d'azote liquide. Des entreprises naissent rapidement (Claude fonde Air liquide, alors que von Linde crée Linde AG et Praxair)[132].
Cet accès à l'élément clé de la décarburation n'échappe pas à Georges Claude qui recommande dès 1910 l'utilisation de l'oxygène pur en sidérurgie. En effet, envisagée dès 1856 par Bessemer[133], l'utilisation d'oxygène pur est une amélioration logique des convertisseurs, le soufflage d'air dans les procédés Bessemer et Thomas montrant des inconvénients évidents :
- 78 % de l'air est composé d'azote et n'a pas de rôle utile dans la décarburation. Cette injection de gaz représente une perte thermique, à peine compensée par le bilan exothermique de l'oxydation du carbone : « chaque m3 d'azote sortant du convertisseur emporte sensiblement la chaleur nécessaire à la fusion d'un peu plus d'un kilogramme de ferraille[134] ».
- la faible teneur en oxygène de l'air ralentit la réaction chimique ; le soufflage dure plus longtemps puisqu'on ne peut pas augmenter les débits sans risquer un débordement ;
- une partie de l'azote reste dissout dans l'acier liquide ; or l'azote est un élément fragilisant pour le fer[Ba 8].
Adaptation des convertisseurs Thomas et Bessemer
[modifier | modifier le code]Le procédé Thomas est le premier à attirer l'attention des chercheurs. En effet, contrairement au procédé Martin, il présente deux inconvénients évidents : l'air est injecté froid[note 24] et il traverse la charge de part en part[Ba 9]. Son réglage thermique est délicat : la température du bain, chauffé par l'oxydation du carbone, augmente moins vite que le point de fusion du métal qui s'appauvrit régulièrement en carbone[note 4]. C'est l'oxydation du silicium et du phosphore, ou l'utilisation d'une fonte plus chaude et plus chargée en carbone qui permet en fait la fusion. Ce constat amène à des pratiques paradoxales : pour pouvoir décarburer et déphosphorer, il devient nécessaire d'avoir une quantité minimale de ces éléments indésirables[132].

Le remplacement simple de l'air par de l'oxygène pur présente cependant des difficultés considérables. La réaction de l'oxygène pur avec la fonte mène à des températures de 2 500 à 2 700 °C : dans ces conditions, sans refroidissement des tuyères, le fond d'un convertisseur est détruit en quelques heures. Entre 1937 et 1940, Lellep, à Oberhausen dans la Ruhr, essaie en laboratoire des tuyères en cuivre refroidies à l'eau : suffisante pendant la décarburation, cette solution ne tient pas en phase de déphosphoration, sans compter la dangerosité de ce refroidissement à l'eau, qui fait renoncer à des essais en aciérie[136].
L'enrichissement de l'air en oxygène représente donc une solution de transition qui est explorée dès les années 1920. En 1925, à Oberhausen encore, l'enrichissement du vent en oxygène est essayé dans un convertisseur Thomas. En 1930, la première grande installation de distillation des gaz de l'air permet à la Maximilianshütte à Sulzbach-Rosenberg de souffler ses convertisseurs au vent enrichi[137],[Ba 9]. Après la Seconde Guerre mondiale, le procédé est essayé plus largement en Europe. Celui-ci permet de doper la production des aciéries à un moment où il faut alimenter les usines construites grâce au plan Marshall.
On ne se contente pas de mélanger l'oxygène avec de l'air. Pour dépasser 40 % d'oxygène, il faut des diluants plus adaptés que l'azote : le dioxyde de carbone est essayé à Domnarvet en Suède en 1947-1949[138], la vapeur d'eau est essayée vers 1950 en France et en Allemagne, puis adoptée dans le Pays de Galles en 1958[note 25]. L'amélioration est sensible, mais les chercheurs savent mal comment exploiter le pouvoir refroidissant de la vapeur et du CO2, qui procède d'un autre mécanisme : le craquage à haute température[note 26].
Adaptation du convertisseur Martin
[modifier | modifier le code]Le four Martin, par principe peu handicapé par l'azote de l'air, ne justifiait pas le même empressement de la part des chercheurs. Les expériences d'utilisation d'oxygène ne commencent qu'en 1946 aux États-Unis et au Canada[142], [143], mais l'industrialisation de l’enrichissement à l'oxygène s'opère dès la fin des années 1950, simultanément sur tous les types de convertisseurs. Ce délai, dû au manque de capacité de production d'oxygène, masque une mise au point rapide : l'injection d'oxygène se fait au-dessus du bain, ce qui fait disparaître la problématique du refroidissement de la tuyère.
Le procédé Martin, dont la polyvalence et l'aptitude aux affinages poussés lui ont permis de fabriquer plus de 70 % de l'acier mondial produit entre 1930 et 1960, va encore pousser son avantage vis-à-vis des convertisseurs Bessemer et Thomas. En effet, la décarburation de la fonte s'y faisait grâce à l'oxygène contenu dans un lit de minerai de fer déposé sur la sole avant la versée de la fonte. L'usage de l'oxygène augmente la température de flamme et son impulsion : elle devient capable de décarburer la fonte sans recourir au minerai.
À partir de 1960, l'injection d'oxygène va se généraliser. Elle se fait au moyen d'une lance semblable à celle que les Autrichiens développent dans le cadre de leurs recherches sur les convertisseurs à oxygène pur.
Le convertisseur à l'oxygène pur : le type LD
[modifier | modifier le code]L'idée de combiner un soufflage d'oxygène par le haut, tel que développé sur le four Thomas, avec une cornue Bessemer-Martin n'a rien de séduisant : il semble difficile d'obtenir une pénétration du jet d'oxygène dans le bain d'acier liquide (de densité 7) sans générer d'énormes remous et fumées.
Ce n'est donc qu'après avoir constaté les limites d'une amélioration des procédés existants, que les premiers essais de soufflage à l'oxygène pur démarrent. Le métallurgiste suisse Robert Durrer démontre l’intérêt économique du procédé. Le , il réalise la première coulée d'acier affiné à l'oxygène, avec un soufflage latéral[144]. Il conseille Theodor Suess qui, à Linz, améliore le procédé choisissant une lance pénétrant verticalement dans la cornue[132]. Le , les essais commencent.

Les résultats sont déconcertants pour les chercheurs : contraints d'éloigner la lance de la surface à cause de ses fréquents bouchages, il ne constatent pas pour autant une dégradation de ses performances[144]. Les essais continuent avec des charges de plus en plus importantes. Le procédé s'avère très prometteur : dès la fin de l'année 1949, soit six mois après le premier essai, les prototypes apparaissent plus économiques que les meilleurs convertisseurs classiques[132].
La même année, l'usine de Linz, engagée dans un profond processus de réorganisation, doit construire une aciérie pour alimenter son nouveau laminoir à chaud[note 27]. Audacieuse, l'entreprise opte pour le nouveau procédé qui n'existe que depuis quelques mois. Quelques kilomètres plus loin, l'usine de OAMG de Donawitz, qui procède aux mêmes essais, lance également en 1950 la construction d'une aciérie à l'oxygène avec soufflage par lance émergée. Les deux sociétés, qui ont chacune demandé indépendamment un brevet s'entendent et le nom du procédé change de Linz Düsenstahl (« lance de Linz ») pour Linz-Donawitz[132].
Le procédé s'étend : dès 1951, les métallurgistes japonais s'initient au nouveau procédé. L'invention est en effet radicale : plus efficaces et donc moins nombreux que leurs équivalents à l'air, les nouveaux convertisseurs ne demandent qu'un investissement environ deux tiers et des coûts d'exploitation limités à 55 % de ceux d'une usine classique de capacité comparable[146]. L'acier obtenu montre en outre d'excellentes qualités métallurgiques : il se travaille mieux à froid que l'acier Martin, ce qui le rend plus apte à être tréfilé ou laminé à froid[147]. Les concurrents européens, qui ont mené de nombreuses recherches dans la même direction, contestent longuement aux deux aciéries la paternité exclusive de l'invention. Aux États-Unis, plusieurs sociétés acquièrent le savoir-faire autrichien puis refusent d'acquitter les redevances, ne reconnaissant pas la validité du brevet et allant jusqu'à faire modifier la loi américaine sur les brevets, alors en cours de procédure, en [148].

C'est que, contrairement à leurs collègues, Durrer et Suess ont compris que le brassage du métal liquide est en fait assuré par les bulles de monoxyde de carbone issues de la décarburation :
« Dans le procédé LD, l'oxygène est soufflé vers le bain depuis une lance verticale, refroidie par eau, dont l'extrémité en cuivre est percée de cinq à sept tuyères convergentes-divergentes. La pression de soufflage, d'environ 20 bars, détermine une vitesse d'éjection de l'ordre de 700 m/s, c'est-à-dire la vitesse du Concorde. La hauteur de lance varie au cours de l'affinage. Traversant la couche de laitier, l'oxygène réagit immédiatement et entièrement avec le fer de la fonte, donnant un monoxyde de fer liquide, lui-même immédiatement réduit par le silicium et le carbone présents. La silice formée est neutralisée par la chaux versée à l'enfournement et contribue à former le laitier qui surnage au-dessus du métal, et mousse sous l'effet du dégagement gazeux jusqu'à remplir presque entièrement le convertisseur. Ce dégagement de CO au point d'impact chasse également les couches superficielles du bain vers le bord, faisant monter de nouvelles masses de métal des profondeurs de la cornue[132]. »
— Olivier Bisanti, Un siècle d'oxygène en sidérurgie
La conversion à l'oxygène produit cependant de grandes quantités de fumées rousses (oxyde de fer), très chaudes et riches en monoxyde de carbone. La mise au point du procédé va donc nécessiter la construction de coûteux systèmes de dépoussiérage. L'encombrement des hottes et des cheminées, la complexité de leur gestion (toute entrée d'air provoquant une combustion du monoxyde de carbone pouvant détruire la cheminée) impose la construction d'aciéries neuves, dont la hauteur permet d'y loger le système de dépoussiérage. En contrepartie, les fumées, lavées et dépoussiérées, sont un gaz au fort potentiel énergétique dont l’intérêt va croître après le premier choc pétrolier[132].
Enfin, en supprimant l'azote, l'excédent de chaleur peut être utilisé pour la fusion de ferrailles dans le convertisseur. Les fours à réverbère de Siemens et de Martin deviennent alors inutiles, puisqu'une seule installation devient capable d'affiner la fonte comme de recycler les ferrailles ; de plus, la ferraille est généralement moins chère que la fonte issue des hauts fourneaux, surtout si celle-ci vient des chûtages faits sur les installations en aval de l'aciérie.
Autres convertisseurs à l'oxygène pur
[modifier | modifier le code]Avec le convertisseur LD, le brassage est assuré par la montée de bulles de monoxyde de carbone issues de la décarburation. Mais ce mouvement, efficace en début de soufflage, tend à ralentir lorsque le carbone dissous passe en dessous de 0,1 %, et le brassage avec le laitier diminue corrélativement.
L'histoire se répète : comme le convertisseur de Bessemer, le process LD révolutionne la sidérurgie mais se révèle inadapté à la déphosphoration. En effet, l'oxydation du phosphore ne se produit qu'après le départ de tout le carbone, et l'élimination de l'oxyde P2O5 nécessite un brassage énergique avec la chaux du laitier.
L'apparition du procédé LD ne va donc pas stopper les développements[149]. D'autres convertisseurs à l'oxygène vont apparaître, tous très différents :
- les convertisseurs à soufflage latéral, comme les fours Kaldo, où le brassage de l'acier liquide est assuré par la rotation de la cornue, imitant la cinématique d'une bétonnière. La lance à oxygène n'ayant plus à assurer le brassage, celle-ci est positionnée loin du bain, et oxyde ainsi les fumées à l'intérieur même de la cornue. La chaleur due à la combustion du monoxyde de carbone est récupérée par l'acier[150]. Ne nécessitant pas de dépoussiérage et d'un excellent rendement thermique, cette technologie a cependant disparu, à cause du coût prohibitif de renouvellement des réfractaires, soumis à des chocs thermiques répétés[151].
- les convertisseurs à soufflage par le bas. C'est la compréhension du rôle de la vapeur ou du dioxyde de carbone lors des essais de dilution de l'oxygène injecté dans les convertisseurs Thomas et Bessemer qui permet la mise au point de ce procédé. L'oxygène est injecté pur, mais la tuyère en cuivre est refroidie par une injection périphérique d'hydrocarbures qui, en arrivant au contact du métal liquide, vont subir un craquage suffisamment endothermique pour éviter la fusion du cuivre[136]. Le soufflage intégral par le bas est efficace mais délicat.
La disparition progressive de ces procédés, spécialisés dans la conversion des fontes phosphoreuses, n'est pas uniquement due à leur défauts intrinsèques. C'est l'importation de minerais plus riches et sans phosphore, devenue économique grâce à la baisse des coûts d'extraction et de transport, qui va précipiter l'abandon des minerais historiquement exploités. En effet, une haute teneur en fer limite la fusion d'une gangue stérile au haut fourneau (c'est-à-dire la consommation de coke) et l’absence de phosphore réduit la consommation de chaux au convertisseur. Dans ce contexte, ces procédés disparaissent mais lèguent leur amélioration au convertisseur LD :
- le Kaldo a montré l’intérêt d'utiliser la lance à oxygène pour réaliser une combustion partielle des fumées dans la cornue, ce qui permet d’augmenter le recyclage de ferrailles[150],[104] ;
- les tuyères de soufflage par le fond ont été adoptées comme moyen de brassage métallurgique au convertisseur LD : ce brassage est devenu incontournable à l'élaboration de nouveaux alliages. Près de 15 % des convertisseurs disposent en 2002 d'un soufflage mixte lance-tuyère[152], les 85 % restants étant à soufflage intégral par le haut, dont la simplicité reste un avantage évident.
Un nouveau modèle technico-économique : l'aciérie électrique
[modifier | modifier le code]Dès 1810, Humphry Davy avait démontré expérimentalement la possibilité de fondre le fer avec un arc électrique. Le XIXe siècle voit plusieurs ingénieurs tenter d'industrialiser ce procédé : en 1878-79, William Siemens dépose un brevet pour un type de four à arc. Les premiers fours à arc électrique modernes sont mis au point par Paul Héroult, en France, avant d'être construits dans une usine aux États-Unis en 1907. En 1922, l'énergie électrique française coûte exactement le double de celle obtenue par la combustion du coke : l'avenir du four électrique n'y est envisagé que dans la production d'alliages spéciaux[F 10]. Vers 1950, la modernisation des réseaux électriques favorise cependant l’apparition d’usines où des fours électriques puissants se substituent aux hauts fourneaux et convertisseurs[153].

Le four électrique simplifie notablement la chaîne de production.
Dans le milieu des années 1960 apparaissent près de Brescia, dans le Piémont en Italie, de très petites aciéries où une vingtaine d’employés refondent des ferrailles d’importation pour produire des ronds à béton à très bas coût. Mais l’expansion de la filière électrique, fondée sur la simplicité de l’usine, impose aussi que les outils avals puissent être simplifiés : de petits laminoirs flexibles[note 27] sont progressivement développés. En 1966, l'entreprise américaine Nuclear Corporation of America décide d'assurer ses approvisionnements en acier en rachetant quelques aciéries. Quelques années plus tard, l'entreprise devient NUCOR, ses débouchés sur l'équipement militaire perdant de l'intérêt devant l'importance de sa branche sidérurgique et surtout ses perspectives de croissance[154]. De fait, NUCOR vient de théoriser un concept révolutionnaire : l'aciérie électrique compacte, la mini-mill[153].
Alors que les sidérurgistes traditionnels poursuivent la course au gigantisme des installations[155], et pensent avoir verrouillé l'accès au marché en soumettant la production d'acier à la capacité de gérer des investissements gigantesques, NUCOR contourne l'utilisation des hauts fourneaux en dédiant des fours électriques à la fusion de ferrailles de récupération. En aval du four, une coulée continue produit l'acier à la section la plus proche possible du produit final (brames minces pour l'obtention de tôles, section en « os de chien » pour les poutrelles…), puis quelques outils de laminage assurent le parachèvement[153].
En effet, à cette époque, la phase d'équipement des États-Unis étant finie, beaucoup de ferraille devient disponible, la récupération à l'aimant rendant la collecte économique. Ce mélange de ferrailles refondues donne un acier de qualité médiocre, mais largement suffisante pour la plupart des applications dans le bâtiment ou l'industrie. En implantant des petites unités neuves et proches des centres de consommation, l'entreprise s'affranchit également de la mainmise des puissants syndicats de la métallurgie, qui règnent dans les vieux centres industriels proches des mines[153].
La fulgurante ascension de NUCOR qui, tablant sur la mise au point d’aciers de plus en plus techniques sans renoncer à l’aciérie compacte, devient le premier sidérurgiste américain en deux décennies, remet en question la filière sidérurgique :
- les sidérurgistes positionnés sur les produits les moins techniques, soit disparaissent, soit remplacent leurs hauts fourneaux par des fours électriques. Ce genre d'adaptations atteint cependant rarement la compétitivité d'une usine neuve et conçue dès l'origine autour d'un four électrique[156] ;
- les parts de marché perdues mènent à des restructurations, d'autant plus douloureuses que la sidérurgie avait mal anticipé la stabilisation de la demande d'acier ;
- les hauts fourneaux migrent à proximité des gisements les plus riches : c'est la « sidérurgie sur l'eau » avec, en France, les constructions des complexes de Fos-sur-Mer et de Dunkerque fonctionnant à partir de minerais importés[157].
Malgré les ambitions de ces nouveaux entrants, la filière électrique apparaît à la fin des années 1990 comme complémentaire aux traditionnels hauts fourneaux[153]. Elle excelle sur les marchés des :
- aciers courants utilisés dans l'électroménager, le bâtiment ou l'emballage qui tolèrent parfois des alliages pollués par des éléments fragilisants (cuivre, nickel, chrome et vanadium), que l'on ne sait pas ôter de l'acier liquide ; les produits longs, comme les poutrelles ou les barres deviennent quasi exclusivement produits à partir de ferrailles récupérées ;
- aciers spéciaux (aciers inoxydables, aciers pour forge…) où la flexibilité du four électrique correspond aux faibles quantités produites.
Les aciers destinés aux emboutissages profonds ou aux sollicitations sévères (applications cryogéniques, réservoirs haute pression…) restent issus des hauts fourneaux, la qualité du minerai de fer étant plus facile à maîtriser que celles des ferrailles.
Évolutions récentes ou à venir
[modifier | modifier le code]Les techniques de production de l'acier ont donc évolué par grandes étapes au cours desquelles des procédés complémentaires ont coexisté : fonte de haut fourneau et affinage, fonte au coke et fer puddlé, acier élaboré à la cornue ou sur sole, four électrique ou aciérie à l'oxygène. Ces inventions ont été à chaque fois des bouleversements pour l'ensemble de la sidérurgie.

Le coût énergétique et l'évolution des sources d'approvisionnement ont motivé cette succession de couples d'outils. À un moment donné, le choix d'un procédé se justifie alors à la fois par la matière première disponible, c'est-à-dire le minerai (selon sa teneur en phosphore ou sa compatibilité avec le haut fourneau) ou les ferrailles, ainsi que par l'énergie disponible. Pour la sidérurgie contemporaine, si le soufflage à l'oxygène pur s'impose à la fois dans les pays émergents et dans les métallurgies les plus exigeantes en termes d'impuretés chimiques, la filière électrique remplace l'affinage de la fonte dès que la quantité ou la qualité des ferrailles disponibles le permet[A 3].
Malgré ces innovations, la production de l'acier n'a pas échappé à la course à la réduction des frais fixes, menée grâce à l'augmentation de la taille des aciéries. La sidérurgie est devenue ainsi l'exemple typique de l'industrie lourde. Mais l’amélioration de la productivité a été également permise par la spécialisation des outils[104],[note 28]. En effet, le procédé Siemens - Martin, qui assurait 80 % de la production mondiale en 1950, a été remplacé par des outils optimisés, soit pour fondre, soit pour convertir la fonte en acier. De plus, ces nouveaux outils se révèlent peu adaptés à la maîtrise complète de la composition chimique : c'est ainsi qu'est apparue progressivement la métallurgie en poche, un ensemble d'outils spécialisés dans l'obtention d'alliages[A 4].
Il reste qu'au début du XXIe siècle, les principales préoccupations de la sidérurgie rejoignent celles des autres industries lourdes, comme la chimie ou la production d'électricité :
- limiter l'impact environnemental, par des installations pouvant coûter jusqu'à 20 % du coût d'une usine neuve[A 5]. La production d'une tonne d'acier entraîne en outre le rejet d'au moins deux tonnes de dioxyde de carbone[130] ;
- s'adapter aux matières premières : l'importation de minerais riches et facilement fusibles a permis l'expansion de la sidérurgie japonaise[A 6]. Mais à plus long terme, l'épuisement des meilleurs gisements (en termes de richesse comme d'accès) est prévisible, même si l'abondance du fer et le recyclage repoussent souvent cette perspective ;
- diminuer le coût énergétique, le coke et l'électricité restant des sources d'énergies coûteuses[note 29].
Notes et références
[modifier | modifier le code]Notes
[modifier | modifier le code]- La définition précise et scientifique de l'acier a été définitivement établie et admise à la fin du XIXe siècle.
- La découverte d'objets en fer à un endroit n'excluant pas que d'autres puissent être trouvés ailleurs
- Pour Huang Zhanyue et Donald B. Wagner, qui soulignent les contradictions et l'indigence de nombreuses déclarations, le bas fourneau a probablement précédé le haut fourneau en Chine. La présence précoce d'objets en fonte est plus facile à attribuer à la refonte d'une loupe produite au bas fourneau, qu'à la mise au point d'un four de réduction-fusion comme le haut fourneau. L'apparition de la fonderie en Europe pourrait avoir aussi suivi le même chemin au XIVe siècle[26],[27].
- Le liquidus d'une fonte à 6 % de carbone est de l'ordre de 1 150 °C, et passe à 1 500 °C lorsque l'on approche la composition du fer pur.
- L'illustration montre un procédé d'affinage de la fonte liquide par brassage en présence d'air et de poudre (wuchaoni). Adolf Ledebur et Donald B. Wagner rejettent le fait que la poudre soit de la wustite mais proposent du salpêtre, plus courant, broyable et très oxydant. Un tel procédé est alors très différent du puddlage[31].
- 20 siècles après les Chinois, Réaumur préconisera la méthode de cofusion de fer et de fonte pour obtenir de l'acier… sans succès car les européens sont incapables de produire de manière économique une fonte de qualité suffisante[SF 2].
- Si on ajoute, à un mélange ferreux, jusqu'à 6 % de phosphore, la température de fusion descend jusqu'à 950 °C.
- Composé tautologique dont le premier composant a été emprunté à l'iranien oriental *aspēn « fer » (cfr. sogdien ’spn-, Khwarezm ’spny, ossète æfsǽn, pachto ōspana) tandis que le second, hérité, signifie « fer ».
- Dans son livre Metallum Martis, Dudd Dudley revendique avoir produit de la fonte au coke de bonne qualité dès 1622. Mais, faute d'autres sources, il n'est pas possible d'évaluer sa technique.
- La modération de Neilson fut mal récompensée : il dut attendre 1843 pour toucher ses royalties, après un long procès au Tribunal Écossais d'Édimbourg
- Le vent chaud facilitant aussi la conduite du haut fourneau, il est devenu possible d'utiliser d'autres matières. D'après Thomas Turner, l'invention de Neilson permit la valorisation du minerai écossais et l'expansion de la sidérurgie écossaise, qui passa d'une production annuelle de 37 500 tonnes en 1830 à 200 000 tonnes en 1840. L'utilisation de vent chaud permit également l'utilisation d'anthracite aux États-Unis, où aucun charbon cokéfiable n'avait encore été découvert (brevet de F. W. Gessenhainer en 1836).
- Cet argument, partiellement inexact, montre la méconnaissance qu'avaient alors les scientifiques des réactions chimiques dans le haut fourneau : non seulement la transformation du CO2 en CO est endothermique, mais elle ne peut se passer que si la température augmente, ce qui n'est vrai qu'au centre du four et non au-dessus des tuyères.
- Les gaz sont prélevés par des ouvertures ménagées dans l'épaisseur de la cuve, et collectés dans une conduite circulaire. Les charges qui se trouvent au-dessus de ces ouvertures servent alors de fermeture.
- Les fontes blanches, contenant peu de silicium, sont les plus faciles à décarburer. Mais elles sont aussi plus résistantes et difficiles à obtenir que les grises, ce qui en fait des fontes chères.
- Les précurseurs Cort et Rogers ont vieilli dans la pauvreté alors que Hall, en achevant l'amélioration du puddlage, put vivre confortablement de son invention.
- Le puddlage sec est appelé ainsi par le fait que la fonte blanche est peu visqueuse et que la sole, peu fusible, génère peu de laitier.
- Le taux de carbone du mélange diminuant, la température restant constante dans le four, la température de fusion étant du type eutectique, la température de fusion du mélange augmente (voir le diagramme de phase fer-carbone ci-dessus) provoquant une augmentation de la viscosité.
- Selon la tradition populaire, Walker s'était déguisé en un mendiant en haillons, qui ne demandait qu'à se réchauffer aux feux de la forge pendant une froide nuit d'hiver[98].
- Le four à réverbère utilisé pour le puddlage est en effet trop rudimentaire pour fondre facilement le fer. Il est nécessaire de le doper par des améliorations diverses pour qu'il fonctionne bien au-delà de 1 500 °C.
- Plus d'un siècle après l'invention, ce constat n'a pas changé. La seule amélioration sensible apportée aux convertisseurs modernes consiste en un trou de vidange latéral, distinct du bec de la cornue.
- À cause de leur minerai insuffisamment phosphoreux, l’intérêt des sidérurgistes américains pour le procédé Thomas reste mesuré : en 1880, Thomas refuse de vendre ses droits pour 150 000 £ aux maîtres de forges wesphaliens, mais les cède 55 000 £ aux Américains en 1881[Cr 6].
- Après l'annexion du bassin ferrifère, les Français découvrent le gisement de Briey, d'une teneur en fer de 36 % à 40 % contre 30 % en moyenne dans la Moselle annexée. Quoiqu'un peu plus difficile d'accès, la minette française est donc la plus avantageuse et est massivement exportée en Allemagne[F 8].
- Il est essentiel de bien distinguer les capacités de production de la production réelle. En effet, de nombreuses unités n'ont jamais atteint leur capacité de production théorique, et beaucoup d'autres sont utilisées de manière épisodique, lorsque la conjoncture rend leur fonctionnement rentable.
- Le procédé de soufflage du convertisseur avec un air préchauffé, assez complexe, n'a été breveté qu'en 1935 par les indiens A. M. Malik et S. M. K. Alvi[135]. Il est apparu trop tard pour concurrencer les procédés d'enrichissement à l'oxygène.
- Il s'agit du procédé VLN (Very Low Nitrogen[139]), adopté à Ebbw Vale[140].
- La décomposition thermique de la vapeur commence vers 900 °C pour être totale à 2 500 °C. Celle du dioxyde de carbone commence dès 700 °C. L'injection de vapeur aux tuyères était une méthode connue de réglage thermique de la charge d'un convertisseur Bessemer[141].
- Le laminage à chaud en continu, mis au point aux États-Unis dans les années 1930, a été importé en Europe par le Plan Marshall. Très puissant, son alimentation en lingots, brames ou blooms entraîne la concentration de la production dans quelques aciéries géantes[145].
- L'élaboration des aciers inoxydables se fait dans des aciéries spécialisées, en faisant notamment appel à un convertisseur spécifique, le type AOD, dont le principe se rapproche du type LD. La mise au point de ce convertisseur est liée à celle de l'élaboration du ferrochrome au four électrique : ces développements sortent du domaine de cet article.
- De 1955 à 1975, la consommation spécifique de coke d'un haut fourneau a pu être divisée par deux grâce à l'injection de charbon et la préparation du minerai. Quant aux fours électriques, des brûleurs ou des installations de préchauffage de ferrailles diminuent leur dépendance à l’électricité.
Références
[modifier | modifier le code]- A. Bailly, Dictionnaire grec-français, Hachette,
- Strabon, traduction française par Amédée Tardieu, Géographie, t. 12, Paris, Hachette, (lire en ligne), chap. 3 (« Le Pont »), p. 20
- Pline l'Ancien, Histoire naturelle [détail des éditions] [lire en ligne] : Livre VII
- περί των μεταλλευομένων - Lisez Péri ton metalleuomenon
- Assimilé à tort par l'Encyclopédie de Diderot et D'Alembert à un fleuve d’Espagne dont l'eau favoriserait la trempe ; voir Denis Diderot et Jean le Rond D'Alembert, Encyclopédie ou Dictionnaire raisonné des sciences, des arts et des métiers, t. 1, Paris, 1751-1772 (lire en ligne), Acier
- (en) Michiel de Vaan, Etymological dictionary of Latin and the other Italic languages, Leiden Boston, Brill, , 825 p. (ISBN 978-90-04-32189-2, OCLC 969947419), p. 214
- René-Antoine Ferchault de Réaumur, L'art de convertir le fer forgé en acier et l'art d'adoucir le fer fondu : Ou de faire des Ouvrages de fer fondu aussi finis que de fer forgé, Paris, Michel Brunet, , 568 p. (lire en ligne)
- Gaspard Monge, Description de l'art de fabriquer des canons, Imprimerie du comité de salut public, an ii (1793-1794) de la république française (lire en ligne), p. 11
- Guy Murry, Métallurgie de base à l'usage des utilisateurs de métaux, Paris, PYC Livres, , 171 p. (ISBN 2-911008-24-3), p. 126
- « Famille indo-européenne », sur axl.cefan.ulaval.ca (consulté le ).
- Jacques Freu et Michel Mazoyer, Les Hittites et leur histoire, des origines à la fin de l'ancien royaume, t. I, Paris, Harmattan, , 429 p. (ISBN 978-2-296-04392-3 et 2-296-04392-5, lire en ligne), p. 30
- (en) Richard Cowen, « The Age of Iron, Chapter 5, in a series of essays on Geology, History, and People prepares for a course of the University of California at Davis », University of California at Davis (consulté le ).
- Hamady Bocoum (dir.), Aux origines de la métallurgie du fer en Afrique : Une ancienneté méconnue. Afrique de l'Ouest et Afrique centrale, UNESCO, , 240 p., 16x24cm (ISBN 978-92-3-203807-4, présentation en ligne)
- Philippe Fluzin, « Des vestiges métallurgiques trouvés en Afrique, et l’apparition de la sidérurgie recule de deux siècles », En direct, le journal de la recherche et du transfert de l'arc Jurassien, Université de Franche-Comté, no 224, (lire en ligne)
- Caroline Robion-Brunner et al., chap. 18 « L'Afrique des métaux », dans François-Xavier Fauvelle (dir.), L'Afrique ancienne : De l'Acacus au Zimbabwe, Belin, coll. « Mondes anciens », , 678 p. (ISBN 978-2-7011-9836-1).
- (en) Xander Veldhuijzen, « History of iron production », .
- (en) Jane C. Waldbaum, From Bronze to Iron : the transition from the Bronze Age to the Iron Age in the eastern Mediterranean, Göteborg : Paul Aströms, , 106 p.
- (en) Anthony M. Snodgrass, The Coming of the Age of Iron, New Haven ; London, Theodore A. Wertime and James D. Mulhy, , 555 p. (ISBN 0-300-02425-8 et 0-300-02425-8), « Iron and Early Metallurgy in the Mediterranean », p. 336-337
- (en) Paul T. Craddock, Early Metal Mining and Production, Edingburgh, Prentice Hall & IBD, , 383 p. (ISBN 978-1-56098-535-8), p. 258-259
- (en) Peter Roger Stuart Moorey, Ancient mesopotamian materials and industries : The archaeological evidence, Winona Lake (Ind.), Eisenbrauns, , 419 p. (ISBN 1-57506-042-6 et 978-1575060422, lire en ligne), « Metalworking », p. 288
- Charles Virolleaud, « Les nouveaux textes alphabétiques de Ras-Shamra (XVIe campagne, 1952) », Annales. Économies, Sociétés, Civilisations, vol. 30 fascicule 3-4, no 2, , p. 187-195 (lire en ligne)
- Paul Courbin, « Etudes dans la Grêce Archaïque : Valeur comparée du fer et de l'Argent lors de l'introduction du monnayage », Annales. Économies, Sociétés, Civilisations, vol. 14, no 2, , p. 209-233 (lire en ligne)
- Sylvain Bauvais, « Prolégomènes à une histoire de la métallurgie du fer au Levant Sud », Bulletin du Centre de recherche français à Jérusalem, no 19, (lire en ligne)
- ArcelorMittal Fos/mer, Jean-Paul Guichard d'Arenc, « L'histoire de l'acier ».
- (en) Lothar von Falkenhausen, « The Waning of the Bronze Age: Material Culture and Social Developments, 770-481 B.C. », dans Michael Loewe et Edward L. Shaughnessy (dir.), The Cambridge History of Ancient China, From the Origins of Civilization to 221 BC, Cambridge, Cambridge University Press, , p. 539
- (en) Donald B. Wagner, « The earliest use of iron in China », .
- (en) Donald B. Wagner, Iron and Steel in Ancient China, Leiden, E. J. Brill, , 573 p. (ISBN 978-90-04-09632-5 et 9004096329, lire en ligne), p. 48 ; 264
- (en) Robert Temple (préf. Joseph Needham), The Genius of China : 3,000 Years of Science, Discovery, and Invention, New York, Simon and Schuster, , 254 p. (ISBN 0-671-62028-2), p. 49-50
- (en) Patricia Buckley Ebrey, Anne Walthall et James B. Palais, East Asia : A Cultural, Social, and Political History, Boston, Houghton Mifflin, , 652 p. (ISBN 0-618-13384-4), p. 30
- « Le génie scientifique de la Chine », Le courrier de l'UNESCO, sur unesco.org, UNESCO, , p. 10.
- (en) Donald B. Wagner, « Iron Production in three Ming Texts : Tie ye zhi, Guangdong xinyu, and Tian gong kai wu », 22 mai 2003 (révisions mineures le 18 juin 2003).
- Adrienne R. Weill, « Métallurgie », dans Encyclopædia Universalis
- [PDF](en) William Lox, « Bintie: the wootz steel in ancient China », 13 janvier 2009 (révision le18avril 2009).
- (en) Donald B. Wagner, The state and the iron industry in Han China, NIAS Press, , 148 p. (ISBN 87-87062-77-1 et 9788787062770, lire en ligne), p. 80-84 cité dans Iron Production in three Ming Texts[31]
- Michèle Pirazzoli-t'Serstevens et Marianne Bujard, Les dynasties Qin et Han : Histoire générale de la Chine (221 av. J.-C. - 220 ap. J.-C., Paris, Les Belles Lettres, , 511 p. (ISBN 978-2-251-44638-7), chap. 5 (« L'Empire : gouvernement, économie, voies de communication »), p. 204.
- (en) Joseph Needham et Donald B. Wagner, « Ferrous metallurgy », dans Science and Civilisation in China, vol. 11, Cambridge University Press, , 477 p. (ISBN 0521875668 et 9780521875660, lire en ligne), p. 31
- (zh) Wang Zhen, Livre d'agriculture, (lire sur Wikisource)
- (zh) Song Yingxing, Tiangong Kaiwu, , voir aussi l'illustration
- Ye Fan, Livre des Han postérieurs., coll. « Encyclopedia of China », ve siècle
- (en) Liu Haiwang, « A large oval shaped blast furnace of the Han dynasty : excavated recently in Henan, China », HMS NEWS Historical Metallurgy Society, no 48, (lire en ligne)
- Maurice Burteaux, « Le tatara », Soleil d'acier, .
- Oleg Sherby et Jeffrey Wadsworth, « Les aciers de Damas », Pour la science, , p. 58-64 (lire en ligne)
- Madeleine Durand-Charre, Les aciers damassés : Du fer primitif aux aciers modernes, Paris, Mines Paris ParisTech Les Presses, coll. « Collection histoire et sociétés », , 206 p. (ISBN 978-2-911762-87-1 et 2-911762-87-8, lire en ligne), p. 83
- Georges Emeriau, « Histoire de la métallurgie du fer et de l'acier damas », (consulté le ).
- « Le cimeterre » (consulté le ).
- (en) Matthew V. Veazey, « 1 600 Years Young : Thanks to its Enduring Corrosion Resistance, an Indian Historical Artifact’s Appearance Belies its Age », Materials Performance, Chemistry International, (lire en ligne)
- (en) Josef Riederer et Ralf-B. Wartke, « Iron », dans Brill's New Pauly, Hubert Cancik, Helmuth Schneider, Manfred Landfester : Brill, (ISSN 1574-9347)
- Édouard Fourdrignier, « L'âge du ferà la fin du : Halstatt - Le Marnien - La Têne », Bulletin de la Société préhistorique française, vol. 1, no 6, , p. 207-215 (lire en ligne)
- Homère (trad. Leconte de Lisle), Iliade, Paris, Lemerre, , 465 p. (lire en ligne), « Chant 23 »
- Gilbert Kaenel, « Civilisation de La Tène » dans le Dictionnaire historique de la Suisse en ligne. consulté le 2 juillet 2010
- J.E. Rehder, « Iron versus bronze for Edged Tools and weapons. A metallurgical view », JOM, , p. 42-46
- Ovide, « Métamorphoses 14.712 », sur Itinera Electronica.
- (en) Paul T. Craddock, Mining and Metallurgy, Oxford University Press cité dans (en) John Peter Oleson, The Oxford Handbook of Engineering and Technology in the Classical World, Oxford, Oxford university press, , 865 p. (ISBN 978-0-19-518731-1), p. 108
- (en) Donald B. Wagner, The State and the Iron Industry in Han China, Copenhague, Nordic Institute of Asian Studies Publishing, , 148 p. (ISBN 87-87062-77-1, lire en ligne), p. 73
- Rolf Sprandel, La production du fer au Moyen Âge, vol. 24, coll. « Annales. Économies, Sociétés, Civilisations », (lire en ligne), chap. 2, p. 305-321
- (en) Thomas Woods, How the Catholic Church Built Western Civilization, Washington, D.C., Regnery Publ., (ISBN 0-89526-038-7), p. 35-37
- (en) David Derbyshire, « Henry "Stamped Out Industrial Revolution" », The Daily Telegraph, cité par T. Woods
- (de) Robert Durrer, Grundlagen der Eisengewinnung, Berne, Verlag Francke AG, , p. 56-58
- (de) Otto Johannsen, Geschichte des Eisens, Dusseldorf, Verlag Stahleisen mbH, , 3e éd., p. 133
- (en) Julius H. Strassburger, Dwight C. Brown, Terence E. Dancy et Robert L. Stephenson, Blast furnace : Theory and practice, vol. 1, New-York, Gordon and Breach Science Publishers, , 275 p. (ISBN 0-677-13720-6, lire en ligne), p. 5–8
- (de) Verein Deutscher Eisenhüttenleute, Gemeinfassliche Darstellung des Eisenhüttenwesens, Dusseldorf, Stahleisen mbH, 1970/71, 17e éd., p. 7
- (en) A. R. Lucas, « Industrial milling in the ancient and Medieval Worlds », Technology and Culture, vol. 46, , p. 19 (DOI 10.1353/tech.2005.0026)
- Olivier Guyotjeannin et Guillaume Balavoine, Atlas de l'histoire de France IXe – XVe siècle, Paris, Autrement, , 103 p. (ISBN 2-7467-0727-6 et 978-2-74-670727-6), p. 31
- Laurent Theis, Histoire du Moyen Âge français, Perrin, , 400 p., p. 304-305
- Joëlle Burnouf, Danielle Arribet-Deroin, Bruno Desachy, Florence Journot, Anne Nissen-Jaubert, Manuel d'archéologie médiévale et moderne, Armand Colin, , p. 355
- Roland Eluerd, Les Mots du fer et des Lumières : Contribution à l'étude du vocabulaire de la sidérurgie française (1722-1812), Paris, Honoré Champion, coll. « Bibliothèque de littérature moderne », , 524 p. (ISBN 2-85203-318-6, OCLC 231616930), p. 192
- (en) Jockenhövel, Albrecht et al., « Archaeological Investigations on the Beginning of Blast Furnace-Technology in Central Europe », Abteilung für Ur- und Frühgeschichtliche Archäologie, Westfälische Wilhelms-Universität Münster, résumé dans : (en) A. Jockenhövel, « Archaeological Investigations on the Beginning of Blast Furnace-Technology in Central Europe », dans Peter Crew and Susan Crew, Early Ironworking in Europe: Archaeology and Experiment: Abstracts of the International Conference at Plas Tan y Bwlch 19–25 September 1997, Snowdonia National Park Study Centre, Gwynedd, Wales, (OCLC 470699473, présentation en ligne), Plas Tan y Bwlch Occasional Papers No 3, p. 56–58.
- (en) Bert Hall, « Medieval Iron and Steel - Simplified », Institute for the History and Philosophy of Science and Technology, University of Toronto.
- [PDF](sv) Catarina Karlsson, Marie Pettersson Jensen et Jonas Ros, « Lapphyttans masugn : Undersökning av grundkonstruktionen under den medeltida masugnen », Stiftelsen Kulturmiljövård, .
- (en) A. Wetterholm, Blast furnace studies in Nora bergslag, Järn och Samhälle, Örebro universitet, (ISBN 91-7668-204-8)
- [PDF] Ludwig Eschenlohr, « Artisanat et industrie du fer dans le nord-ouest de la Suisse du 9e au 14e siècle », dans Habitat et mobilier archéologiques de la période entre 800 et 1350 : Actes du Colloque « Archéologie du Moyen Age en Suisse », Bâle, Archéologie Suisse AS, Groupe de travail suisse pour l’archéologie du Moyen Age et de l’époque moderne SAM, Association suisse Châteaux forts SBV, (ISBN 978-3-908006-57-2, lire en ligne), p. 306
- (de) « Montanarchäologie im Bergischen Land », Geschichtsverein Rösrath, .
- Edmond Truffaut, « Le Fer du Sauerland », sur manganeseandsteel.fr, .
- (en) Donald B. Wagner, Science and Civilisation in China : 5. Chemistry and Chemical Technology : part 11 Ferrous Metallurgy : (suite de Joseph Needham), Cambridge University Press, , p. 349–351 ; 354-355
- (en) B. G. Awty, « The blast furnace in the Renaissance period: haut fourneau or fonderie? », Transactions of Newcomen Society, vol. 61, 1989–90, p. 67
- Monge, an II (1793-1794), p. 11
- (en) B. Awty, C. Whittick et P. Combes, The Lordship of Canterbury, iron-founding at Buxted, and the continental antecedents of cannon-founding in the Weald, coll. « Sussex Archaeological Collections » (no 140), , p. 71–81
- Encyclopédie méthodique, t. 2, Paris, Panckoucke (1re éd. 1783) (lire en ligne), Arts et métiers mécaniques, « Fer (art du), Gosses forges, Acier », p. 542
- Francis Dabosi, « La forge à la Catalane : magie de l'Eau et du Feu », sur cadrescatalans.com.
- « La fabrication de l'acier », L'industrie, Village de Poissons, (consulté le ).
- Robert Halleux, Anne-Catherine Bernès, Luc Étienne, « L'évolution des sciences et des techniques en Wallonie », Atouts et références d’une région, Institut Destrée, (consulté le ).
- P.-F. de Dietrich, Description des gîtes de minerai, des forges et des salines des Pyrénées […], Didot et Cuchet, , 600 p., p. 533
- Grüner et Lan, 1862, p. 422
- (en) K. C. Barraclough, Steelmaking before Bessemer : Blister Steel, the birth of an industry, The Metals Society, , p. 48-52
- Arthur Birembaut, « Réaumur et l'élaboration des produits ferreux », Revue d'histoire des sciences et de leurs applications, vol. 11, no 2, , p. 140-141
- (en) Thomas Southcliffe Ashton, Iron and Steel in the Industrial Revolution, Manchester, Manchester University Press, , 252 p. (lire en ligne), Letter from Mrs. Abiah Darby, circa. 1775, p. 249-252
- (en) Philip Riden, « The Output of the British Iron Industry before 1870 », The Economic History Review, , p. 442–459
- J.-F. Bocquillon et M. Mariage, Économie générale : première G, Paris, Bordas, , 212 p. (ISBN 2-04-018961-0), p. 9.
- (en) William F. Durfee, « The development of American industries since Colombus », Popular Science, vol. 38, .
- (en) Frank William Taussig, Some Aspects of the Tariff Question, Cambridge, MA, Harvard University Press, (réimpr. 1972) (1re éd. 1915), 528 p. (ISBN 978-0-404-06348-1 et 0-404-06348-9, lire en ligne), III Iron and steel, chap. 9 (« A Survey of Growth »), p. 4-7
- (en) Robert Chambers, Biographical Dictionary of Eminent Scotsmen, Blackie and Son of Glasgow, (lire en ligne)
- [PDF](en) A. G. Romanenko, Hot-blast stoves - 120 years, Plenum Publishing Corporation, (DOI 10.1007/bf01087865, lire en ligne)
- Walter de Saint-Ange et V. Le Blanc, Métallurgie pratique du fer : Description méthodique des procédés de fabrication de la fonte et du fer, Librairie scientifique et industrielle de L. Mathias (Augustin), 1835-1836 (lire en ligne), p. 70
- (en) « The Final Slag and Slag–Metal Interactions », steeluniversity.org (consulté le ).
- William Henry Greenwood, Steel and Iron : Comprising the practice and theory of the several methods pursued in their manufacture, and of their treatment in the rolling mills, the forge, and the foundry, , 546 p. (ISBN 1-110-38645-1, lire en ligne)
- (en) Henry Hartshorne et al. (ill. B. Howard Rand), Household Cyclopedia of General Information…, New York, (lire en ligne), chap. 15 (« Metallurgy »), p. 609
- (en) Samuel Smiles, Industrial Biography, , 160 p. (lire en ligne), p. 53-60
- (en) Dictionary of National Biography, Londres, Smith, Elder & Co, 1885–1900 (lire sur Wikisource), Huntsman, Benjamin
- « Sheffield's industrial history », sur sheffieldontheinternet.co.uk.
- (en) P.T. Craddock, Early Metal Mining and Production, Edinburgh university press, , p. 283
- (en) Ralph Anstis, Man of Iron, Man of Steel : Lives of David and Robert Mushet, Albion House, , 216 p. (ISBN 0-9511371-4-X), p. 140, 147
- Emmanuel-Louis Grüner et Charles-Romain Lan, État présent de la métallurgie en Angleterre, Paris, Dunod éditeur, (lire en ligne), p. 825
- (en) The journal of the Iron and Steel Institute, vol. XCI, Londres, , 711 p. (lire en ligne), « Statistics », p. 655-657
- Jean Duflot, Encyclopædia Universalis (lire en ligne), « Sidérurgie »
- (en) Hermann Wedding (trad. from the german by: William B. Phillips, Ph.D. & Ernst Prochaska), Wedding's basic Bessemer process [« Basische Bessemer - oder Thomas-Process »], New York Scientific Publishing Company, , 224 p. (lire en ligne), p. 28-42
- Ramona-Nicoleta Borşa, Thèse de doctorat : Élaboration de poudres et de dépôts de phosphates de calcium silicatés à usage de biomatériaux, Université de Toulouse, (lire en ligne), « Diagramme de phases du système Ca0 - P2O5 [Kreidler1967] »
- (en) R.W. Burnie, Memoir and letters of Sidney Gilchrist Thomas, Inventor, John Murray, (lire en ligne), p. 119-120 ; 108-110 ; 120-121
- (en) Lance Day et Ian McNeil, Biographical Dictionary of the History of Technology, Routledge, (1re éd. 1996) (ISBN 0-8493-9163-6 et 978-0849391637, lire en ligne), « Thomas, Sidney Gilchrist »
- Alexis Aron, « Les conséquences économiques de l'invention de Sidney Gilchrist Thomas (allocution) », La revue de métallurgie, no 12, , p. 18-22
- "Quand l’innovation engendre l’incertitude : réception et diffusion du procédé Martin", par Jean-Philippe Passaqui. Éditions du Marteau Pilon, 2013, [1]
- (en) « The interactive Ellingham diagram », sur doitpoms.ac.uk, University of Cambridge, .
- (en) William Henry Greenwood, Steel and Iron : Comprising the practice and theory of the several methods pursued in their manufacture, and of their treatment in the rolling mills, the forge, and the foundry, , 546 p. (ISBN 1-110-38645-1, lire en ligne), p. 213-217
- [PDF] (en) W. H. Voskuil et H. E. Risser, Economics Aspects of Direct Reduction of Iron Ore in Illinois, Urbana (Illinois), Division of the Illinois Geological Survey, (lire en ligne)
- À la même époque, la production d'une tonne de fonte en fusion nécessite typiquement 740 kilos de charbon de bois[L 30] ou 1 100 kilos de coke[L 31]
- (en) « Direct reduction: a review of commercial processes », EPA (United States Environment Protection Agency, , p. 9.
- Entre 1950 et 1975, on recense 1 200 brevets, 100 procédés sont analysés, 12 principes essentiels sont testés[115]…
- [PDF](en) « Process technology followed for sponge iron », Environment Compliance Assistance Centre (ECAC).
- (en) J. Bilika, P. Pustejovskab, S. Brozovac, S. Jursova, « Efficiency of hydrogen utilization in reduction processes in ferrous metallurgy », Scientia Iranica, vol. 20, , p. 337–342 (lire en ligne)
- [PDF](en) « 4000 Years Later… a history of the direct reduction of iron ore », Hylsa, .
- Cette unité inaugure le procédé HYL I. D'une capacité initiale de 75 000 tonnes annuelles, elle a produit du minerai préréduit jusqu'en 1991[119].
- [PDF](en) Best Available Techniques (BAT) Reference Document for Iron and Steel Production, Direction régionale de l'environnement, de l'aménagement et du logement, , 597 p. (lire en ligne), p. 523-202
- [PDF](en) « World direct reduction statistics », Midrex, .
- En 2006, 92 % du minerai préréduit était issu de procédés utilisant le gaz naturel[121]. Mais, depuis 2010, cette proportion n'est plus que de 75 %[122].
- (en) « Tenova HYL », Tenova Group.
- Société Chimique de France, « Le fer »(Archive.org • Wikiwix • Archive.is • Google • Que faire ?).
- (en) Alexander Lyman Holley, Siemens' direct process of making wrought iron from ore, in a rotating gas furnace, , 21 p.
- [PDF](en) « World direct reduction statistics », Midrex, .
- « Minerai de fer & acier » [archive du ], CNUCED.
- (en) Amit Chatterjee, Sponge Iron Production By Direct Reduction Of Iron Oxide, PHI Learning Private Limited, , 353 p. (ISBN 978-81-203-3644-5, lire en ligne)
- (en) « Site officiel du programme ULCOS », ULCOS.
- Marc Magain, « La réduction directe passe au charbon : Le belge Sidmar envisage d'investir dans la première installation industrielle européenne de réduction directe du minerai de fer par le charbon. », L'Usine Nouvelle, no 2653, (lire en ligne)
- Olivier C. A. Bisanti, « Un siècle d'oxygène en sidérurgie », Soleil d'acier, .
- (en) F. Wallner et E. Fritz, « Fifty years of oxygen-converter steelmaking », Revue de Métallurgie, no 10, , p. 825-837
- H. Lecompte, Cours d'aciérie, Éditions de la Revue de métallurgie, , 309 p.
- « Brevet du convertisseur à air chaud », Office Européen des Brevets.
- Leroy et al., « Soufflage d'oxygène pur par le procédé LWS », La revue de métallurgie,
- P. Leroy et E. Devernay, « Essais de soufflage au convertisseur Thomas… l'air enrichi… l'oxygène », La revue de métallurgie,
- Kalling et al., « Emploi d'oxygène-acide carbonique au lieu d'air pour le soufflage final dans le procédé Thomas », La revue de métallurgie,
- (en) James Albert Allen, Studies in Innovation in the Steel and Chemical Industries, Manchester University Press, , 246 p. (ISBN 0-678-06790-2 et 978-0678067901), p. 130
- (en) Robert Protheroe-Jone, Welsch steel, , 60 p. (ISBN 0-7200-0424-1, lire en ligne), p. 50
- (en) Bradley Stoughton, Ph.B., B.S., The metallurgy of iron and steel, New York, McGraw-Hill Book Company, , 509 p. (lire en ligne), p. 105
- F. Kerry, « Les premiers résultats de l'emploi de l'oxygène dans les aciéries », La revue de métallurgie,
- G. Husson, « Emploi de l'oxygène en sidérurgie, état actuel de la question et vues d'avenir », La revue de métallurgie,
- (en) Vaclav Smil, Transforming the twentieth century : Technical Innovations and Their Consequences, t. 2, New York, Oxford University Press, , 358 p. (ISBN 0-19-516875-5 et 9780195168754, lire en ligne), p. 97-99
- Jean-Yves Debost et Bernard Réal, Les rapports des industries de la manutention avec l'évolution des processus de production et des moyens de transport dans le cours de l'internationalisation du capital, Université des Sciences Sociales de Grenoble, Institut de Recherche Economique et de Planification, (lire en ligne [PDF]), partie 2, p. 47-64
- (de) Roman Sandgruber, « Das LD-Verfahren erobert die Welt (Les LD conquièrent le monde) », Oberösterreichische Nachrichten, (consulté le ).
- (en) James C. O. Harris et Mary E. Palfrey, Mineral yearbook, (lire en ligne [PDF]), p. 597
- E. Michaelis, « Histoire de l'évolution et du développement du procédé LD dans le monde », La revue de métallurgie,
- (en) James W. Brock et Kenneth G. Elzinga, Antitrust, the market, and the state : The contributions of Walter Adams, M. E. Sharpe, , 301 p. (ISBN 0-87332-855-8 et 9780873328555, lire en ligne), p. 39
- Colmant et al., « Le procédé KALDO à Sollac », La revue de métallurgie,
- A. Wegscheider, « Etude économique des procédés LD d'affinage des fontes à l'oxygène, comparaison avec le procédé Kaldo », La revue de métallurgie,
- (en) N. Ramaseder, « Technological developments in oxygen converter steelmaking », allbusiness.com, .
- Olivier C. A. Bisanti, « Histoire du four électrique », Soleil d’Acier, .
- « Historique de l'entreprise Nucor », Nucor.
- En 1978, des experts définissaient l'usine rentable de 1990 comme construite sur une voie fonte de capacité annuelle de 20 Mt[A 2]. Mais en 2010, les plus grosses usines sidérurgiques dépassent rarement les 8 Mt/an.
- J-L Pierquin, « Interview de Jean-Louis Pierquin sur la fermeture de l'aciérie de Gandrange », Le Républicain Lorrain, (consulté le ).
- Michel Freyssenet, La sidérurgie française 1945-1979 : L'histoire d'une faillite. Les solutions qui s'affrontent, Paris, Savelli, coll. « Documents critiques », , 241 p. (ISBN 978-2-85930-030-2, OCLC 417353871, BNF 34648522, présentation en ligne, lire en ligne)
- Louis Colombier, Métallurgie du fer, Dunod, , 2e éd. [détail des éditions]
- p. 177.
- p. 191
- p. 211
- p. 212
- p. 235
- Emmanuel-Louis Grüner, Traité de métallurgie, Dunod, 1875 - 1878 [détail des éditions] (Tome 1 et Tome 2)
- t. 2, p. 257
- Tome 1, p. 354
- Tome 1, p. 389
- Tome 1, p. 307
- Tome 2, p. 168
- Tome 2, p. 171.
- Tome 2, p. 199-200.
- Tome 2, p. 257
- Tome 2, p. 240 ; 250-254 ; 257
- Adolf Ledebur (trad. Barbary de Langlade revu et annoté par F. Valton), Manuel théorique et pratique de la métallurgie du fer, Tome I et Tome II, Librairie polytechnique Baudry et Cie éditeur, [détail des éditions]
- p. 381
- p. 320
- p. 183
- p. 36
- p. 440
- p. 452-463
- p. 480-481
- p. 492
- p. 366
- p. 367
- p. 372
- p. 383-384
- p. 386.
- p. 387.
- p. 507
- p. 472
- p. 388
- p. 468
- p. 183-186
- p. 507-508
- p. 513
- p. 548
- p. 545.
- p. 544
- p. 563
- p. 568
- p. 570
- p. 580
- Tome 2, p. 350-352
- Tome 2, p. 82 ; 99-101
- Tome 2, p. 90 ; 99-101
- Tome 2, p. 351
- John Percy (trad. traduction supervisée par l'auteur), Traité complet de métallurgie, t. 4, Paris, Librairie polytechnique de Noblet et Baudry éditeur, (lire en ligne)
- Tome 4, p. 82 ; 488-532
- Tome 4, p. 265-266
- Tome 4, p. 265-276
- Tome 4, p. 266
- Tome 4, p. 35
- Tome 4, p. 254
- Gaspard Monge, Claude Louis Berthollet et Alexandre-Théophile Vandermonde, Avis aux ouvriers en fer sur la fabrication de l'acier, comité de salut public, années 1790 (lire en ligne)
- p. 3
- p. 5
- p. 10
- p. 15
- p. 18
- p. 6
- Jean Gimpel, La Révolution industrielle du Moyen Âge, Seuil, coll. « Points Histoire », , 258 p. (ISBN 2-02-054151-3)
- p. 41
- p. 79
- p. 48
- J. Levainville, L'Industrie du Fer en France, Paris, Armand Colin, coll. « Armand Colin » (no 19), , 210 p. (lire en ligne)
- p. 18
- p. 19-20
- p. 20
- p. 27
- p. 42
- p. 59
- p. 60-62
- p. 167
- p. 99-101
- p. 164-165
- Jacques Corbion (préf. Yvon Lamy), Le savoir… fer — Glossaire du haut-fourneau : Le langage… (savoureux, parfois) des hommes du fer et de la zone fonte, du mineur au… cokier d'hier et d'aujourd'hui, [détail des éditions]
- § Chine
- § Cofusion ; Essence de fer brut ; Procédé de diffusion visco-liquide
- § Terre Noire
- § Four à masse
- § Stückofen
- § Marteau hydraulique
- § Énergie hydraulique
- § Flossofen ; Flussofen ; Fourneau ; Stückofen
- § Haut fourneau (Invention du, Débuts du, Évolution du)
- p. H6
- p. S31
- p. C92
- § Réduction directe
- (en) G. Reginald Bashforth, The manufature of iron and steel, vol. 2 : Steel production, Londres, Chapman & Hall Ltd, , 461 p. (lire en ligne)
- p. 496-497
- p. 33
- p. 329
- p. 434-435
- p. 461-462
- p. 41
- p. 43
- p. 49-54
- p. 55
- (en) Henry Bessemer, Sir Henry Bessemer, F.R.S; An autobiography, [détail des éditions] (lire en ligne)
- p. 138-139
- p. 142
- p. 143
- p. 152 ; 156
- p. 152
- p. 154-163
- p. 148
- p. 334
- p. 144
- p. 157
- p. 172
- p. 136
- p. 171-172
- p. 170
- p. 164
- p. 287-289
- p. 193-194
- p. 200-215
- p. 178-180
- (en) William Tulloch Jeans, The Creators of the Age of Steel, , 356 p. (ISBN 1-4179-5381-0 et 978-1417953813, lire en ligne)
- p. 318-336
- p. 308-309
- p. 303
- p. 304
- p. 309
- p. 316
- p. 310-311
- (en) Thomas Turner (dir.), The metallurgy of iron : By Thomas Turner... : Being one of a series of treatises on metallurgy written by associates of the Royal school of mines, C. Griffin & company, limited, coll. « Griffin's metallurgical series », , 3e éd., 463 p. (ISBN 1-177-69287-2 et 978-1177692878, lire en ligne)
- p. 31
- p. 133-134
- p. 21
- p. 27
- p. 186
- p. 27-28
- p. 28
- p. 191
- p. 347
- p. 350
- p. 42
- p. 49
- Daniel Rivet, L'acier et l'industrie sidérurgique, Paris, Presses universitaires de France, coll. « Que sais-je? » (no 561), , 128 p. [détail des éditions] (ISBN 2-13-035632-X)
- p. 18
- p. 98
- p. 40
- p. 39
- p. 99
- p. 24
Voir aussi
[modifier | modifier le code]Bibliographie
[modifier | modifier le code]- Georges Delbart, « Le centenaire de l’invention du procédé Bessemer », Atomes, no 123, , p. 185-191
- (en) Henry Bessemer, Sir Henry Bessemer, F.R.S; An autobiography, [détail des éditions] (lire en ligne)
- Philippe-Frédéric de Dietrich, Description des gîtes de minerai, des forges et des salines des Pyrénées, suivi d'observations sur le fer mazé et sur les mines des Sards en Poitou, Didot et Cuchet, [détail des éditions] (lire en ligne), partie I
- J. Galey, L. Beaujard, P. Vallet, G. Urbain, J. Tordeux, P. Vilette et J. Foulard, « Mesure et enregistrement de la température du bain au convertisseur Thomas par visée à travers le bec, applications à l'étude de la conversion basique », La Revue de métallurgie, no 11, , p. 69-93
- Emmanuel-Louis Grüner et Charles-Romain Lan, État présent de la métallurgie en Angleterre, Dunod éditeur, (lire en ligne)
- Annie Laurant, Des fers de Loire à l'acier Martin ( maitres de forges en Berry et Nivernais), Royer-saga science,