Geopolymer
![]() | This article has multiple issues. Please help improve it or discuss these issues on the talk page. (Learn how and when to remove these messages)
|
A geopolymer is a vague pseudo-chemical term used to describe inorganic, typically bulk ceramic-like material that forms covalently bonded, non-crystalline (amorphous) networks, often intermingled with other phases. Many geopolymers may also be classified as alkali-activated cements or acid-activated binders. They are mainly produced by a chemical reaction between a chemically reactive aluminosilicate powder e.g. metakaolin or other clay-derived powders, natural pozzolan, or suitable glasses, and an aqueous solution (alkaline or acidic) that causes this powder to react and re-form into a solid monolith. The most common pathway to produce geopolymers is by the reaction of metakaolin with sodium silicate, which is an alkaline solution, but other processes are also possible.[1]
Commercially produced geopolymers may be used for fire- and heat-resistant coatings and adhesives, medicinal applications, high-temperature ceramics, new binders for fire-resistant fiber composites, toxic and radioactive waste encapsulation, and as cementing components in making or repairing concretes. The properties and uses of geopolymers are being explored in many scientific and industrial disciplines such as modern inorganic chemistry, physical chemistry, colloid chemistry, mineralogy, geology, and in other types of engineering process technologies.
The term geopolymer was coined by Joseph Davidovits in 1978 due to the rock-forming minerals of geological origin used in the synthesis process.[2] These materials and associated terminology were popularized over the following decades via his work with the Institut Géopolymère (Geopolymer Institute).
Geopolymers are synthesized in one of two conditions:
- in alkaline medium (Na+, K+, Li+, Cs+, Ca2+…)
- in acidic medium (phosphoric acid: H3PO4)
The alkaline route is the most important in terms of research and development and commercial applications. Details on the acidic route have also been published.[3][4]
Composition
[edit]In the 1950s, Viktor Glukhovsky developed concrete materials originally known as "soil silicate concretes" and "soil cements",[5] but since the introduction of the geopolymer concept by Joseph Davidovits, the terminology and definitions of the word geopolymer have become more diverse and often conflicting. The word geopolymer is sometimes used to refer to naturally occurring organic macromolecules;[6] that sense of the word differs from the now-more-common use of this terminology to discuss inorganic materials which can have either cement-like or ceramic-like character.
A geopolymer is essentially a mineral chemical compound or mixture of compounds consisting of repeating units, for example silico-oxide (-Si-O-Si-O-), silico-aluminate (-Si-O-Al-O-), ferro-silico-aluminate (-Fe-O-Si-O-Al-O-) or alumino-phosphate (-Al-O-P-O-), created through a process of geopolymerization.[7] This method of describing mineral synthesis (geosynthesis) was first presented by Davidovits at an IUPAC symposium in 1976.[8]
Even within the context of inorganic materials, there exist various definitions of the word geopolymer, which can include a relatively wide variety of low-temperature synthesized solid materials.[9] The most typical geopolymer is generally described as resulting from the reaction between metakaolin (calcined kaolinitic clay) and a solution of sodium or potassium silicate (waterglass). Geopolymerization tends to result in a highly connected, disordered network of negatively charged tetrahedral oxide units balanced by the sodium or potassium ions.
In the simplest form, an example chemical formula for a geopolymer can be written as Na2O·Al2O3·nSiO2·wH2O, where n is usually between 2 and 4, and w is around 11-15. Geopolymers can be formulated with a wide variety of substituents in both the framework (silicon, aluminium) and non-framework (sodium) sites; most commonly potassium or calcium takes on the non-framework sites, but iron or phosphorus can in principle replace some of the aluminum or silicon.[citation needed]
Geopolymerization usually occurs at ambient or slightly elevated temperature; the solid aluminosilicate raw materials (e.g. metakaolin) dissolve into the alkaline solution, then cross-link and polymerize into a growing gel phase, which then continues to set, harden, and gain strength.
Geopolymer synthesis
[edit]Covalent bonding
[edit]The fundamental unit within a geopolymer structure is a tetrahedral complex consisting of silicon or aluminum coordinated through covalent bonds to four oxygens. The geopolymer framework results from the cross-linking between these tetrahedra, which leads to a 3-dimensional aluminosilicate network, where the negative charge associated with tetrahedral aluminium is balanced by a small cationic species, most commonly an alkali metal cation (Na+, K+ etc). These alkali metal cations are often ion-exchangeable, as they are associated with, but only loosely bonded to the main covalent network, similarly to the non-framework cations present in zeolites.
Oligomer formation
[edit]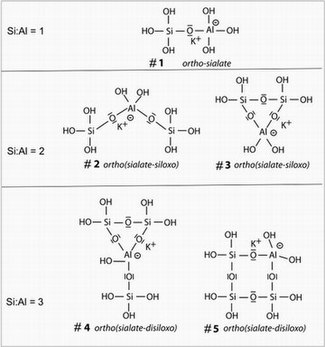
Geopolymerization is the process of combining many small molecules known as oligomers into a covalently bonded network. This reaction process takes place via formation of oligomers (dimer, trimer, tetramer, pentamer) which are believed to contribute to the formation of the actual structure of the three-dimensional macromolecular framework, either through direct incorporation or through rearrangement via monomeric species.[citation needed] These oligomers are named by some geopolymer chemists as sialates following the scheme developed by Davidovits,[2] although this terminology is not universally accepted within the research community due in part to confusion with the earlier (1952) use of the same word to refer to the salts of the important biomolecule sialic acid.[10]
The image shows five examples of small oligomeric potassium aluminosilicate species (labelled in the diagram according to the poly(sialate) / poly(sialate-siloxo) nomenclature), which are key intermediates in potassium-based alumino-silicate geopolymerization. The aqueous chemistry of aluminosilicate oligomers is complex,[11] and plays an important role in the discussion of zeolite synthesis, a process which has many details in common with geopolymerization.
Example of geopolymerization of a metakaolin precursor, in an alkaline medium[12]
The reaction process broadly involves four main stages:
- Alkaline hydrolysis of the layered structure of the calcined kaolinite
- Formation of monomeric and oligomeric species
- In the presence of waterglass (soluble potassium or sodium silicate), cyclic Al-Si structures can form (e.g. #5 in the figure), whereby the hydroxide is liberated by condensation reactions and can react again
- Geopolymerization (polycondensation) into polymeric 3D-networks.
The reaction processes involving other aluminosilicate precursors (e.g. low-calcium fly ash, crushed or synthetic glasses, natural pozzolans) are broadly similar to the steps described above.
Geopolymer 3D-frameworks and water
[edit]
Geopolymerization forms aluminosilicate frameworks that are similar to those of some rock-forming minerals, but lacking in long-range crystalline order, and generally containing water in both chemically bound sites (hydroxyl groups) and in molecular form as pore water. This water can be removed at temperatures above 100 – 200°C. Cation hydration and the locations, and mobility of water molecules in pores are important for lower-temperature applications, such as in usage of geopolymers as cements.[13][14] The figure shows a geopolymer containing both bound (Si-OH groups) and free water (left in the figure). Some water is associated with the framework similarly to zeolitic water, and some is in larger pores and can be readily released and removed. After dehydroxylation (and dehydration), generally above 250°C, geopolymers can then crystallise above 800-1000°C (depending on the nature of the alkali cation present).[15]
Commercial applications
[edit]There exists a wide variety of potential and existing applications. Some of the geopolymer applications are still in development, whereas others are already industrialized and commercialized.[16] They are listed in three major categories:
Geopolymer cements and concretes
[edit]- Building materials (for example, clay bricks)
- Low-CO2 cements and concretes
- Radioactive and toxic waste containment
Geopolymer resins and binders
[edit]- Fire-resistant materials, thermal insulation, foams
- Low-energy ceramic tiles, refractory items, thermal shock refractories
- High-tech resin systems, paints, binders and grouts
- Bio-technologies (materials for medicinal applications)
- Foundry industry (resins), tooling for the manufacture of organic fiber composites
- Composites for infrastructure repair and strengthening
- Fire-resistant and heat-resistant high-tech carbon-fiber composites for aircraft interiors and automobiles
Arts and archaeology
[edit]- Decorative stone artifacts, arts and decoration
- Cultural heritage, archaeology and history of sciences
Geopolymer cements
[edit]![]() | This article contains promotional content. (November 2013) |
From a terminological point of view, geopolymer cement[17] is a binding system that hardens at room temperature, like regular Portland cement.

Geopolymer cement is being developed and utilised as an alternative to conventional Portland cement for use in transportation, infrastructure, construction and offshore applications.[citation needed]
Production of geopolymer cement requires an aluminosilicate precursor material such as metakaolin or fly ash, a user-friendly alkaline reagent[18][promotional source?] (for example, sodium or potassium soluble silicates with a molar ratio (MR) SiO2:M2O ≥ 1.65, M being sodium or potassium) and water (See the definition for "user-friendly" reagent below). Room temperature hardening is more readily achieved with the addition of a source of calcium cations, often blast furnace slag.[citation needed]
Geopolymer cements can be formulated to cure more rapidly than Portland-based cements; some mixes gain most of their ultimate strength within 24 hours. However, they must also set slowly enough that they can be mixed at a batch plant, either for pre-casting or delivery in a concrete mixer. Geopolymer cement also has the ability to form a strong chemical bond with silicate rock-based aggregates.[citation needed]
There is often confusion between the meanings of the terms 'geopolymer cement' and 'geopolymer concrete'. A cement is a binder, whereas concrete is the composite material resulting from the mixing and hardening of cement with water (or an alkaline solution in the case of geopolymer cement), and stone aggregates. Materials of both types (geopolymer cements and geopolymer concretes) are commercially available in various markets internationally.[citation needed]
Alkali-activated materials vs. geopolymer cements
[edit]There exists some confusion in the terminology applied to geopolymers, alkali-activated cements and concretes, and related materials, which have been described by a variety of names including also "soil silicate concretes" and "soil cements".[5] Terminology related to alkali-activated materials or alkali-activated geopolymers is also in wide (but debated) use. These cements, sometimes abbreviated AAM, encompass the specific fields of alkali-activated slags, alkali-activated coal fly ashes, and various blended cementing systems.
User-friendly alkaline-reagents
[edit]
Geopolymerization uses chemical ingredients that may be dangerous and therefore requires some safety procedures. Material Safety rules classify the alkaline products in two categories: corrosive products (named here: hostile) and irritant products (named here: friendly).[citation needed]
The table lists some alkaline chemicals and their corresponding safety labels.[19] Alkaline reagents belonging to the second (less elevated pH) class may also be termed as User-friendly, although the irritant nature of the alkaline component and the potential inhalation risk of powders still require the selection and use of appropriate personal protective equipment, as in any situation where chemicals or powders are handled.
The development of some alkali-activated-cements, as shown in numerous published recipes (especially those based on fly ashes) use alkali silicates with molar ratios SiO2:M2O below 1.20, or are based on concentrated NaOH. These conditions are not considered so user-friendly as when more moderate pH values are used, and require careful consideration of chemical safety handling laws, regulations, and state directives.
Conversely, geopolymer cement recipes employed in the field generally involve alkaline soluble silicates with starting molar ratios ranging from 1.45 to 1.95, particularly 1.60 to 1.85, i.e. user-friendly conditions. It may happen that for research, some laboratory recipes have molar ratios in the 1.20 to 1.45 range.
Examples of materials that are sometimes called geopolymer cements
[edit]Commercial geopolymer cements were developed in the 1980s, of the type (K,Na,Ca)-aluminosilicate (or "slag-based geopolymer cement") and resulted from the research carried out by Joseph Davidovits and J.L. Sawyer at Lone Star Industries, USA, marketed as Pyrament® cement. The US patent 4,509,985 was granted on April 9, 1985 with the title 'Early high-strength mineral polymer'.[20]
In the 1990s, using knowledge of the synthesis of zeolites from fly ashes, Wastiels et al.,[21] Silverstrim et al.[22] and van Jaarsveld and van Deventer[23] developed geopolymeric fly ash-based cements.
Materials based on siliceous (EN 197), also called class F (ASTM C618), fly ashes are known:
- alkali-activated fly ash geopolymer:[24]
- In many (but not all) cases requires heat curing at 60-80°C; not manufactured separately as a cement, but rather produced directly as a fly-ash based concrete. NaOH + fly ash: partially-reacted fly ash particles embedded in an alumino-silicate gel with Si:Al= 1 to 2, zeolitic type (chabazite-Na and sodalite) structures.
- slag/fly ash-based geopolymer cement:[25]
- Room-temperature cement hardening. Alkali metal silicate solution + blast furnace slag + fly ash: fly ash particles embedded in a geopolymeric matrix with Si:Al ~ 2. Can be produced with "user-friendly" (not extremely high pH) activating solutions.
The properties of iron-containing "ferri-sialate"-based geopolymer cements are similar to those of rock-based geopolymer cements but involve geological elements, or metallurgical slags, with high iron oxide content. The hypothesised binder chemistry is (Ca,K)-(Fe-O)-(Si-O-Al-O).[26]
Rock-based geopolymer cements can be formed by the reaction of natural pozzolanic materials under alkaline conditions,[27] and geopolymers derived from calcined clays (e.g. metakaolin) can also be produced in the form of cements.
CO2 emissions during manufacturing
[edit]![]() | This section needs expansion. You can help by adding to it. (April 2024) |
Geopolymer cements may be able to be designed to have a lower attributed emission of carbon dioxide CO2 than some other widely-used materials such as Portland cement.[28] Geopolymers use industrial byproducts/waste containing aluminosilicate phases in manufacturing, which minimizes CO₂ emissions and has a lower environmental impact.[29]
The need for standards
[edit]In June 2012, the institution ASTM International organized a symposium on Geopolymer Binder Systems. The introduction to the symposium states:[citation needed] When performance specifications for Portland cement were written, non-portland binders were uncommon...New binders such as geopolymers are being increasingly researched, marketed as specialty products, and explored for use in structural concrete. This symposium is intended to provide an opportunity for ASTM to consider whether the existing cement standards provide, on the one hand, an effective framework for further exploration of geopolymer binders and, on the other hand, reliable protection for users of these materials.
The existing Portland cement standards are not adapted to geopolymer cements; they must be elaborated by an ad hoc committee. Yet, to do so requires the presence of standard geopolymer cements. Presently, every expert is presenting their own recipe based on local raw materials (wastes, by-products or extracted). There is a need for selecting the right geopolymer cement category. The 2012 State of the Geopolymer R&D,[30] suggested to select two categories, namely:
- type 2 slag/fly ash-based geopolymer cement: fly ashes are available in the major emerging countries;
- ferro-sialate-based geopolymer cement: this geological iron-rich raw material is present in all countries throughout the globe.
along with the appropriate user-friendly geopolymeric reagent.
Health effects
[edit]![]() | This section needs expansion. You can help by adding to it. (April 2024) |
Geopolymers as ceramics
[edit]![]() | This section needs expansion. You can help by adding to it. (April 2024) |
Geopolymers can be used as a low-cost and/or chemically flexible route to ceramic production, both to produce monolithic specimens, and as the continuous (binder) phase in composites with particulate or fibrous dispersed phases.[31]
Room-temperature processed materials
[edit]Geopolymers produced at room temperature are typically hard, brittle, castable, and mechanically strong. This combination of characteristics offers the opportunity for their usage in a variety of applications in which other ceramics (e.g. porcelain) are conventionally used. Some of the first patented applications of geopolymer-type materials - actually predating the coining of the term geopolymer by multiple decades - relate to use in automobile spark plugs.[32]
Thermal processing of geopolymers to produce ceramics
[edit]It is also possible to use geopolymers as a versatile pathway to produce crystalline ceramics or glass-ceramics, by forming a geopolymer through room-temperature setting, and then heating (calcining) it at the necessary temperature to convert it from the crystallographically disordered geopolymer form to achieve the desired crystalline phases (e.g. leucite, pollucite and others).[33]
Geopolymer applications in arts and archaeology
[edit]Because geopolymer artifacts can look like natural stone, several artists started to cast in silicone rubber molds replicas of their sculptures. For example, in the 1980s, the French artist Georges Grimal worked on several geopolymer castable stone formulations.[34]
Egyptian pyramid stones
[edit]In the mid-1980s, Joseph Davidovits presented his first analytical results carried out on samples sourced from Egyptian pyramids. He claimed that the ancient Egyptians used a geopolymeric reaction to make re-agglomerated limestone blocks.[35][36][37] Later on, several materials scientists and physicists took over these archaeological studies and have published results on pyramid stones, claiming synthetic origins.[38][39][40][41] However, the theories of synthetic origin of pyramid stones have also been stridently disputed by other geologists, materials scientists, and archaeologists.[42]
Roman cements
[edit]It has also been claimed that the Roman lime-pozzolan cements used in the building of some important structures, especially works related to water storage (cisterns, aqueducts), have chemical parallels to geopolymeric materials.[43]
See also
[edit]References
[edit]- ^ W.M. Kriven, C. Leonelli, J.L. Provis, A.R. Boccaccini, C. Attwell, V.S. Ducman, C. Ferone, S. Rossignol, T. Luukkonen, J.S.J. van Deventer, J.V. Emiliano, J.E. Lombardi (2024), Why geopolymers and alkali-activated materials are key components of a sustainable world: A perspective contribution. Journal of the American Ceramic Society, https://doi.org/10.1111/jace.19828
- ^ a b An article published by the Commission of the European Communities in 1982 outlines the reasons why the generic term geopolymer was chosen for this new chemistry. See: J. Davidovits, The Need to Create a New Technical Language For the Transfer of Basic Scientific Information, in Transfer and Exploitation of Scientific and Technical Information, Proceedings of the symposium, Luxemburg, 10–12 June 1981, pp. 316-320. http://bookshop.europa.eu/en/transfer-and-exploitation-of-scientific-and-technical-information-pbCD3381271/
- ^ Wagh, A.S. (2004). Chemically Bonded Phosphate Ceramics – A Novel Class of Geopolymers. Proceedings of the 106th annual meeting of the American Ceramic Society, Indianapolis. See also, Chapter 13, Phosphate-based Geopolymers, in J. Davidovits' book Geopolymer Chemistry and Applications.
- ^ Perera, D.S., Hanna, J.V., Davis, J., Blackford, M.G., Latella, B.A., Sasaki, Y. and Vance E.R. (2008). Relative strengths of phosphoric acid-reacted and alkali-reacted metakaolin materials. J. Mater. Sci., 43, 6562–6566.
- ^ a b Gluchovskij V.D. (1959). "Gruntosilikaty" Gosstrojizdat Kiev, Patent USSR 245 627 (1967), Patent USSR 449894 (Patent appl. 1958, granted 1974).
- ^ Kim, D.; Lai, H.T.; Chilingar, G.V.; Yen T.F. (2006). Geopolymer formation and its unique properties, Environ. Geol, 51(1), 103–111.
- ^ See http://www.geopolymer.org/science/introduction
- ^ Pdf-file #20 Milestone paper IUPAC 76 at http://www.geopolymer.org/category/library/technical-papers
- ^ See, Discussion at the Geopolymer Camp 2012, video Geopolymer definition in Wikipedia at http://www.geopolymer.org/camp/gp-camp-2012 Archived 2013-04-15 at archive.today.
- ^ Provis, J.L. and Van Deventer, J.S.J. (2009). Introduction to geopolymers, in: Geopolymers: Structure, Processing, Properties and Industrial Applications, J.L. Provis & Van Deventer (eds.), Woodhead, Cambridge UK, pp. 1–11
- ^ Swaddle, T.W., Salerno, J., and Tregloan, P.A. (1994). Aqueous aluminates, silicates, and aluminosilicates, Chemical Society Reviews, 23 (5), 319–325
- ^ See at http://www.geopolymer.org/science/about-geopolymerization
- ^ Barbosa, V.F.F; MacKenzie, K.J.D. and Thaumaturgo, C., (2000). Synthesis and characterization of materials based on inorganic polymers of alumina and silica: sodium polysialate polymers, International Journal of Inorganic Materials, 2, pp. 309–317.
- ^ Rowles, M.R. (2004). The Structural Nature of Aluminosilicate Inorganic Polymers: a Macro to Nanoscale Study, PhD Thesis, Curtin University of Technology, Perth, Australia.
- ^ Duxson, P.; Lukey, G.C., and van Deventer, J.S.J. (2007). The thermal evolution of metakaolin geopolymers: Part 2 – Phase stability and structural development, Journal of Non-Crystalline Solids, 353, pp. 2186-2200.
- ^ http://www.geopolymer.org/about/business-fellows [bare URL]
- ^ Davidovits, J., (1991). Geopolymers: Inorganic Polymeric New Materials, J. Thermal Analysis, 37, 1633–1656. See also Chapter 24 in Geopolymer Chemistry and Applications, Joseph Davidovits, Institut Géopolymère, Saint-Quentin, France, 2008, ISBN 9782951482050 (3rd ed., 2011).
- ^ See the examples at the Geopolymer Institute page http://www.geopolymer.org/applications/geopolymer-cement
- ^ See in ref. 2
- ^ Davidovits, J. and Sawyer, J.L., (1985). Early high-strength mineral polymer, US Patent 4,509,985, 1985, filed February 22, 1984. The first commercial geopolymer cement was coined Pyrament 2000™ designed for repair and patching operations.
- ^ Wastiels J., Wu X., Faignet S., and Patfoort G. (1994). Mineral polymer based on fly ash, Journal of Resource Management and Technology, 22 (3), 135-141
- ^ Silverstrim, T.; Rostami, H.; Larralde, J.C and Samadi-Maybodi, A. (1997). Fly ash cementitious material and method of making a product, US Patent 5,601,643.
- ^ Van Jaarsveld, J.G.S., van Deventer, J.S.J. and Lorenzen L. (1997). The potential use of geopolymeric materials to immobilize toxic metals: Part I. Theory and Applications, Minerals Engineering, 10 (7), 659–669.
- ^ Palomo, A.; Grutzeck, M.W. and Blanco, M.T. (1999). Alkali-activated fly ashes: a cement for the future, Cement Concrete Res, 29, 1323–1329.
- ^ Izquierdo, M.; Querol, X.; Davidovits, J.; Antenucci, D.; Nugteren, H. and Fernández-Pereira, C., (2009). Coal fly ash-based geopolymers: microstructure and metal leaching, Journal of Hazardous Materials, 166, 561–566.
- ^ Davidovits, J. et al., Geopolymer cement of the Calcium-Ferroaluminium silicate polymer type and production process, PCT patent publication WO 2012/056125.
- ^ Gimeno, D.; Davidovits, J.; Marini, C.; Rocher, P.; Tocco, S.; Cara, S.; Diaz, N.; Segura, C. and Sistu, G. (2003). Development of silicate-based cement from glassy alkaline volcanic rocks: interpretation of preliminary data related to chemical- mineralogical composition of geologic raw materials. Bol. Soc. Esp. Cerám. Vidrio, 42, 69–78. [Results from the European Research Project GEOCISTEM (1997), Cost Effective Geopolymeric Cements For Innocuous Stabilisation of Toxic Elements, Final Technical Report, April 30, 1997, Brussels, Project funded by the European Commission, Brite-Euram BE-7355-93, Jan. 1, 1994 to Feb. 28, 1997].
- ^ Rangan, B.V., (2008). Low-Calcium Fly Ash-Based Geopolymer Concrete, Chapter 26, in Concrete Construction Engineering Handbook, Editor-in-Chief E.G. Nawy, Second Edition, CRC Press, New York.
- ^ Progress in Digital and Physical Manufacturing. Springer Tracts in Additive Manufacturing. 2023. doi:10.1007/978-3-031-33890-8. hdl:10400.8/8622. ISBN 978-3-031-33889-2.
- ^ See the video at http://www.geopolymer.org/camp/gp-camp-2012 Archived 2013-04-15 at archive.today
- ^ Kriven, Waltraud M.; Leonelli, Cristina; Provis, John L.; Boccaccini, Aldo R.; Attwell, Cyril; Ducman, Vilma S.; Ferone, Claudio; Rossignol, Sylvie; Luukkonen, Tero; van Deventer, Jannie S. J.; Emiliano, José V.; Lombardi, Jérôme E. (August 2024). "Why geopolymers and alkali-activated materials are key components of a sustainable world: A perspective contribution". Journal of the American Ceramic Society. 107 (8): 5159–5177. doi:10.1111/jace.19828. ISSN 0002-7820.
- ^ Schwartzwalder, K and Ortman, C.D. (1957), Sodium silicate type cement, U.S. Patent 2,793,956, General Motors Corporation
- ^ Bell, J.L.; Driemeyer, P.; Kriven, W.M. (2009) Formation of ceramics from metakaolin‐based geopolymers: Part I—Cs‐based geopolymer, and Part II-K-based geopolymer, Journal of the American Ceramic Society 92, 1-18 and 607-615
- ^ http://www.geopolymer.org/applications/potential-utilizations-in-art-and-decoration ; also article #19 Dramatized sculptures with geopolymers, at http://www.geopolymer.org/category/library/technical-papers/
- ^ Davidovits, J. (1986). X-Rays Analysis and X-Rays Diffraction of Casing Stones from the Pyramids of Egypt, and the Limestone of the Associated Quarries; pp. 511–20 in Science in Egyptology Symposia, Edited by R. A. David, Manchester University Press, Manchester, U.K. (Pdf-file #A in the Geopolymer Institute Library, Archaeological Papers)
- ^ Davidovits J., (1987). Ancient and modern concretes: what is the real difference? Concrete International: Des. Constr, 9 [12], 23–29.
- ^ Davidovits, J. and Morris, M., (1988). The Pyramids: An Enigma Solved. Hippocrene Books, New York, 1988.
- ^ Demortier, G. (2004). PIXE, PIGE and NMR study of the masonry of the pyramid of Cheops at Giza, Nuclear Instruments and Methods, Physics Research B, 226, 98–109.
- ^ Barsoum, M.W.; Ganguly, A. and Hug, G. (2006). Microstructural Evidence of Reconstituted Limestone Blocks in the Great Pyramids of Egypt, J. Am. Ceram. Soc. 89[12], 3788–3796.
- ^ MacKenzie, Kenneth J.D.; Smith, Mark E.; Wong, Alan; Hanna, John V.; Barry, Bernard and Barsoum, Michel W. (2011). Were the casing stones of Senefru's Bent Pyramid in Dahshour cast or carved? Multinuclear NMR evidence, Materials Letters 65, 350–352.
- ^ Túnyi, I. and El-hemaly, I. A. (2012). Paleomagnetic investigation of the great egyptian pyramids, Europhysics News 43/6, 28-31.
- ^ Klemm, D. and Klemm, R. (2010) The Stones of the Pyramids: Provenance of the Building Stones of the Old Kingdom Pyramids of Egypt, De Gryuter, Berlin/New York, pp. 81-82, and references cited therein
- ^ Davidovits J. and Davidovits F. Geopolymer ’99 Proceedings, 283–295; Davidovits J., Geopolymer Chemistry and Applications, Section 17.4.
External links
[edit]- Geopolymer science. Science Direct. Elsevier. 2024